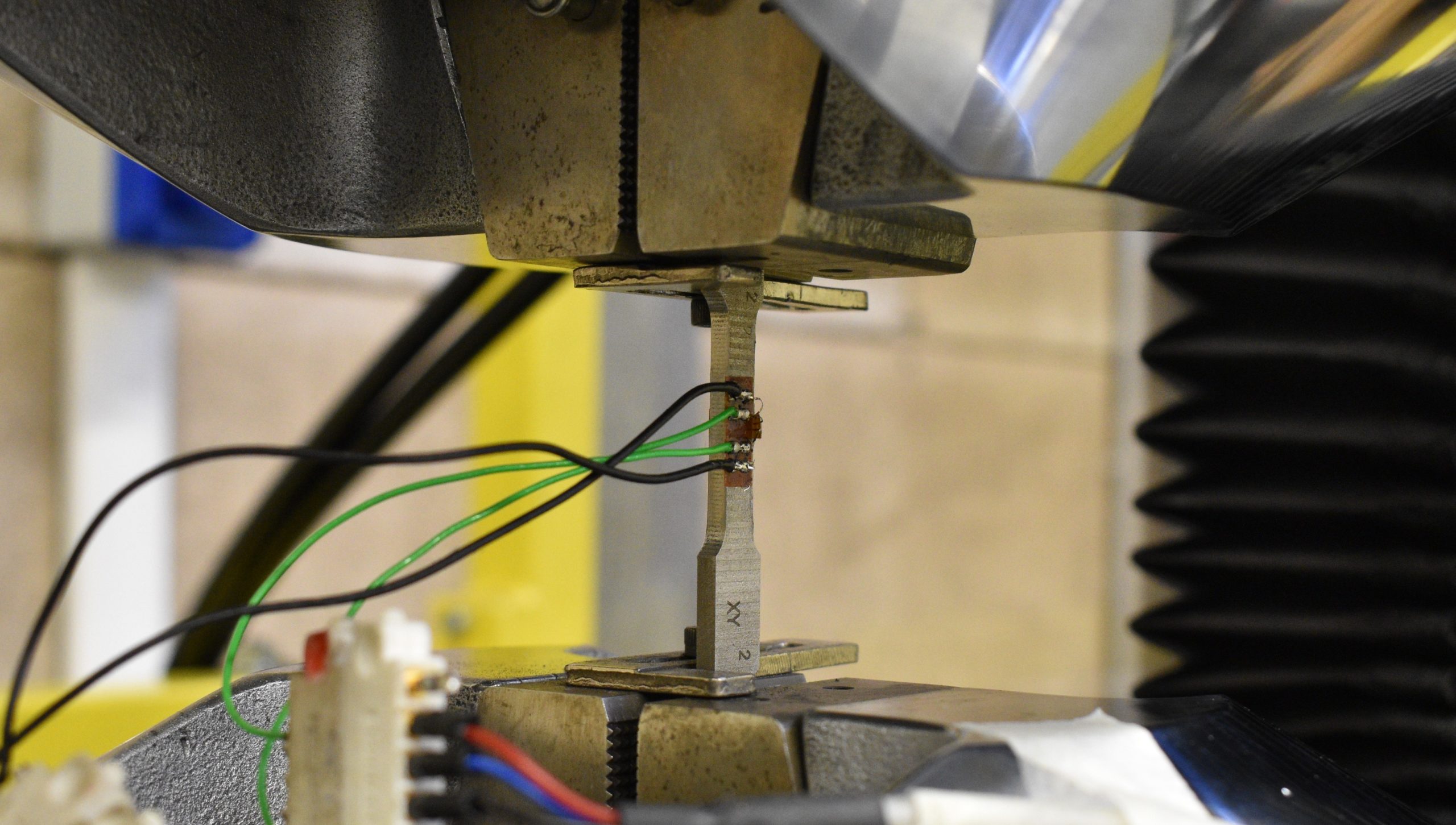
The Politecnico di Milano is leading an international consortium developing metal 3D printing techniques to help construction save energy and cut waste.
The consortium, “ConstructAdd”, believes that printing customised components and joints on-site from scratch will eliminate the scrap produced by cutting parts from an existing steel plate.
Computerised printers that combine heat and metal powders or wire can make precision components with high strength-to-weight ratio, tensile strength, and versatility, they say.
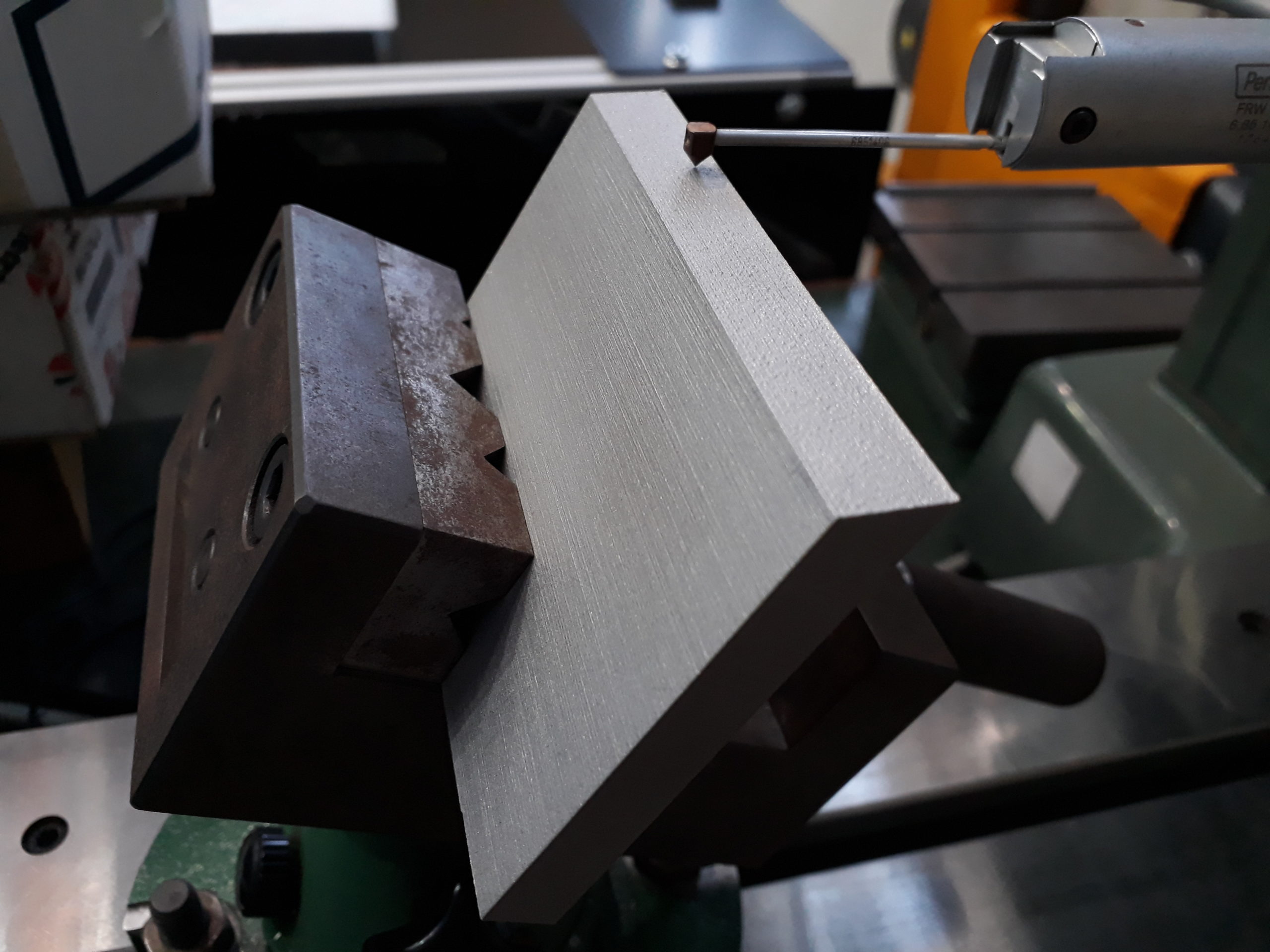
Financed by the European Research Fund for Coal and Steel, ConstructAdd brings together companies, technology, and research centres from five European countries.
It is studying three different printing methods: laser powder bed fusion, wire and arc additive manufacturing, and laser directed energy deposition.
Easily optimised
“Given around one-third of all the waste produced around the world each year comes from the construction industry, steel production has a major role to play here,” said project coordinator Dr. Alper Kanyilmaz of the Politecnico di Milano.
“The current manufacturing techniques available are not easily optimised, and there is a lot of material wasted – for example, during the cutting and welding of steel plates. Also, using conventional construction techniques, a lot of material is used where it isn’t needed and placed in unnecessary spots.”
- Watch a metal component being printed with laser direct energy deposition:
ConstructAdd aims to prove that metal 3D printing can create less waste during fabrication and cut energy consumption by 30%.
“Steel is far more resistant and ductile compared to other materials. So, it offers more opportunities to manufacture more complex geometries which can withstand higher stress and fatigue loads,” said Kanyilmaz.
According to the European Commission, 30% of all waste produced annually in the EU comes from the construction and demolition industry.
Comments
Comments are closed.
Excellent news. Used to dream of being able to lay down the crystal lattice atom by atom as a Process Planning Engineer in the 1970s. I assume that as all these methods still require heat, then as the dendrites form, I’m still going to end up with slip planes and work hardening issues.