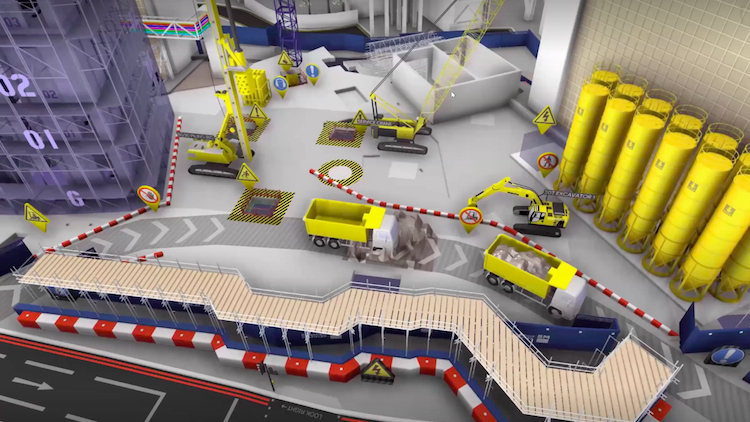
Start early, have as much detail as possible and get the project team on board: these are the three keys to successful implementation of 4D planning, according to James Bowles, founder of 4D specialist Freeform.
Speaking at the Global Construction Summit last week (24 February), Bowles said: “The three things to consider to get the most out of the 4D process are: you want to do it early, ahead of the works; you want to ensure as much content as possible is in the model; and the team must be involved.”
Chris Needham, founder and MD of CSN Project Planning, backed Bowles up: “The earlier you plan something, the earlier you’re going to identify risks and opportunities
You don’t always get great design information at the early stages, but there are past projects and experience you can draw on.
“Once you’ve done a few 4D simulations, you’ve built a library of objects, you know what your set-ups are going to be, the methods you’re going to employ; you can apply those assumptions at an early stage and as you get more information, those assumptions can become more concrete.
“It’s important to get the best information out of the team and speak to the people who have experience, especially for young people who are more likely to be driving this kind of technology.”
Bowles and Needham emphasised the need to embed 4D in a project’s normal processes; the former said: “The 4D model has to be valuable to the people in the room, it has to make sense, it has to sit as part of [existing processes] like safety briefings, planning meetings, etc.”
As well as cost and time savings, Needham highlighted a softer benefit of using 4D: “It promotes better planning – the industry as a whole is not great at planning, especially at the early stage. It’s often done in silos and the information at tender is not necessarily communicated very well to the guys who have got to do it on site – 4D doesn’t solve this, but it helps a great deal.”
Bowles added: “Any project where we’ve done 4D – and there are hundreds now – the project team usually goes forward to the next project and wants 4D again – they don’t go back to the Gantt chart. The project team wants visibility and transparency of what it’s going to build and to get the supply chain on board.”
- Register in seconds to watch this session on demand
Pierpaolo Franco, vice president of international business development at Glodon, agreed: “It empowers the whole team; they can anticipate problems with the design, soft-test and hard-test the model during the construction; but the quality of the data and its input is crucial for success.”
Franco presented a case study of the use of Glodon’s BIM 5D cloud-based platform on the Beijing Olympic Village, built by China Construction First Group.
Measuring 58,110 sq m, the village was built at high altitude on a mountain, creating logistics challenges, and featured a small village relic in the centre that had to be protected, so the planning and simulation had to be exceptionally detailed.
The mountain was scanned to accuracy within 2mm. There was a height difference of 30m to 42m in the east-west direction and the north-south direction of the site.
The challenge that the elevation changes presented for temporary works was overcome, thanks to the three-dimensional visual dynamic planning, with work being carried out in stages. The volume of earthworks was reduced by nearly 60,000 cu m.
The Global Construction Summit is organised by the Chartered Institute of Building and Global Construction Review, in association with Glodon, PlanRadar and Trimble Viewpoint.