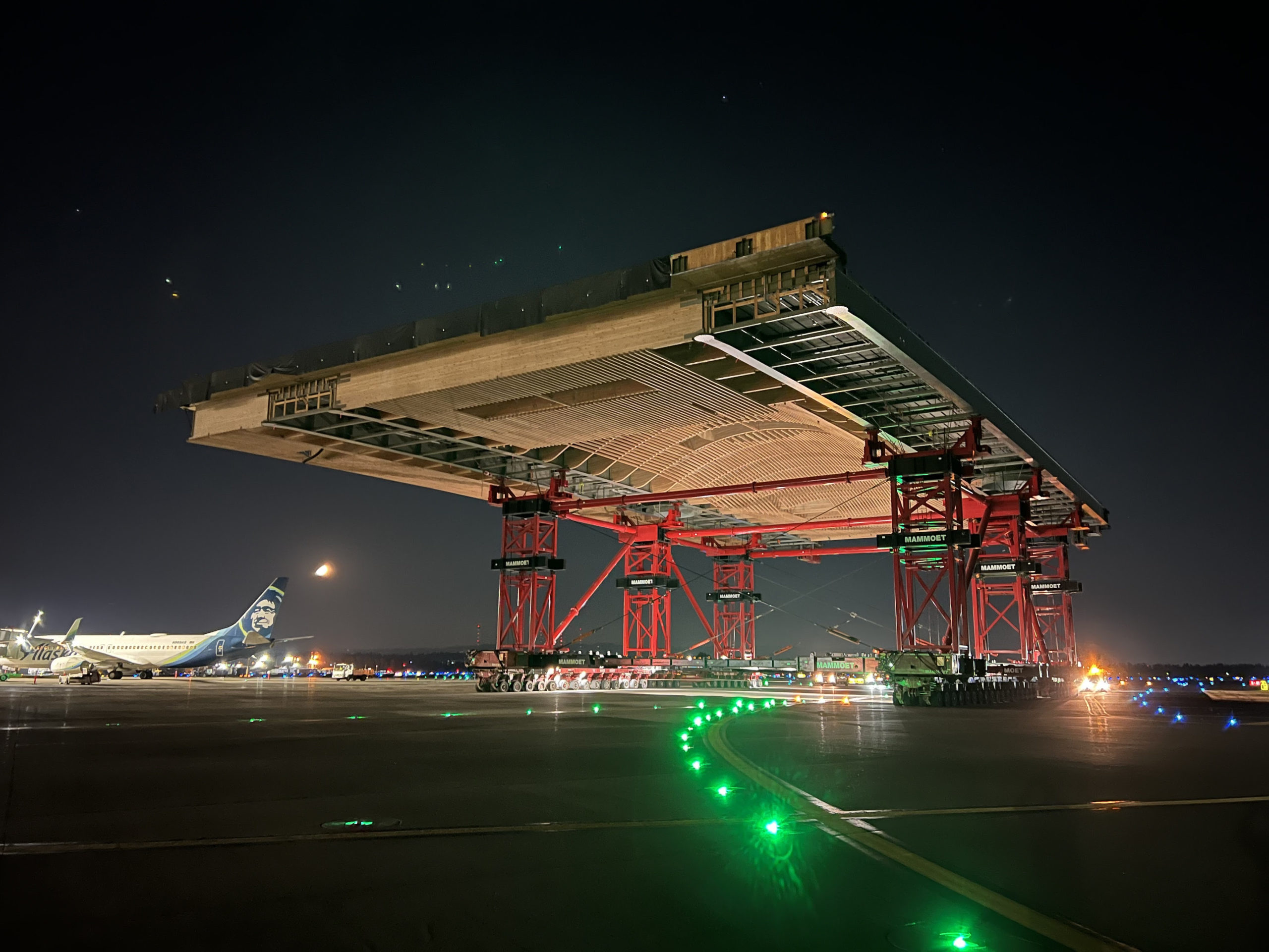
The high-profile expansion of Portland International Airport (PDX) in Oregon has won fame for its vast, wavy roof made largely from Douglas fir from local forests.
The project will nearly double the size of PDX’s main terminal, to be capped by a seismically isolated roof structure over the airport’s central area.
Now, heavy-lift specialist Mammoet has revealed how it is lifting 20 huge roof sections – some the size of football fields weighing up to 632 tons – into place while most people are sleeping.
It was hired to jack up, transport, and install the sections, called “super cassettes”, of five different types while avoiding passenger disruption.
The sections vary in weight between 40 and 632 tons. The biggest spanned 72m in length, 50m wide, and 6m deep.
Build it on the ground first
As the company explains, the roof was prefabricated from locally sourced wood on the ground between the active runways over the course of a year.
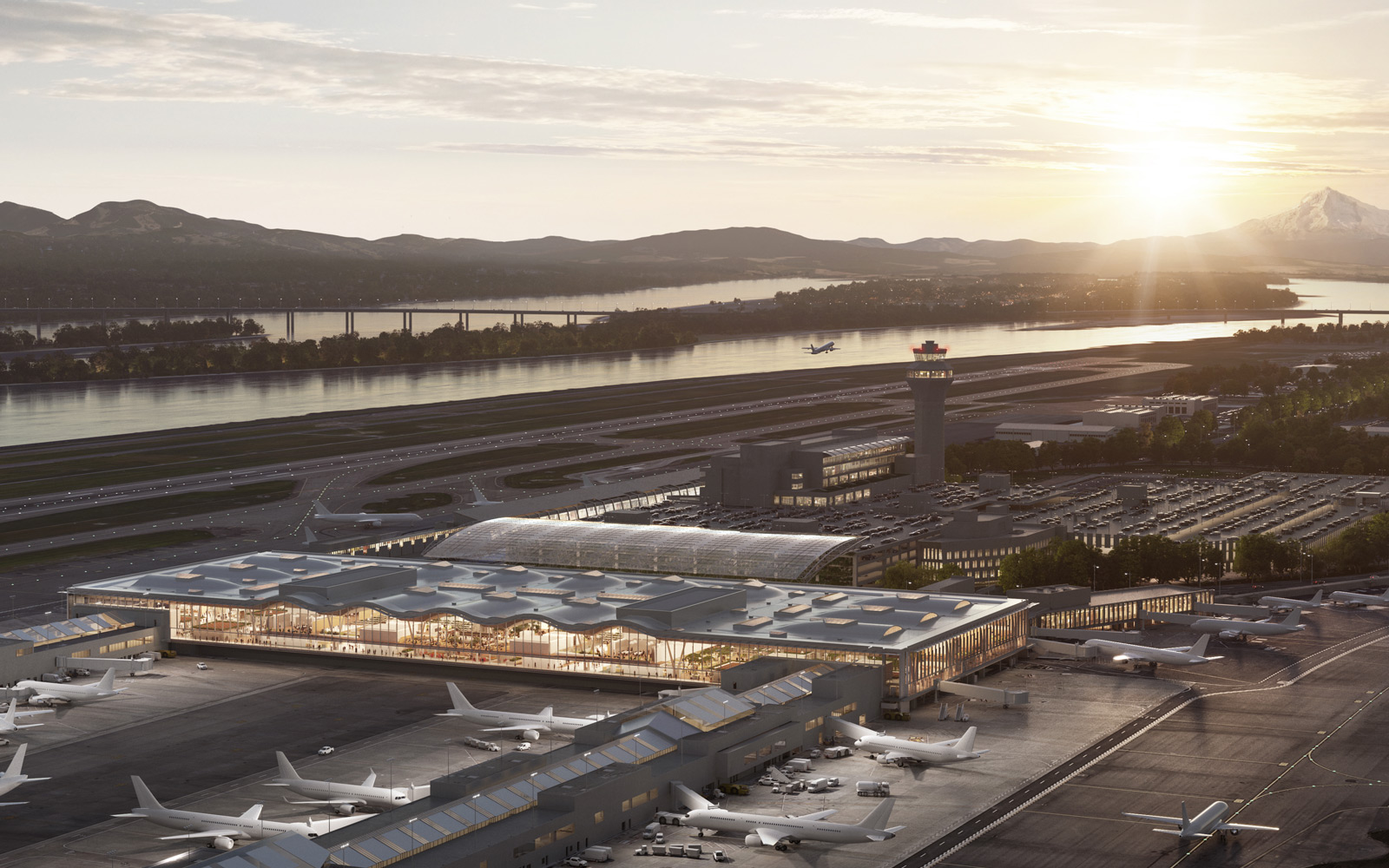
When the time came to install it, the roof was split up into moveable sections.
Depending on the type of section to go next, each was launched, rolled into place, and installed either with self-propelled modular transporters (SPMTs), or lifted with a crane into its final position.
Mammoet used four towers of Mega Jack 800 to jack up the roof panels to approximately 17m so the SPMTs with falsework could drive underneath
Countdown to midnight
At midnight on the day of each move, the runways were closed for the section’s one-mile trip from assembly yard to terminal, with the SPMT rolling along at 1mph.
Most sections needed to be installed over the top of populated areas of the existing terminal, so when a section was going up, the affected area had to be closed.
Each section was installed using stationary skidding propelled by strand jacks and lowered with the skidding jacks onto column isolators.
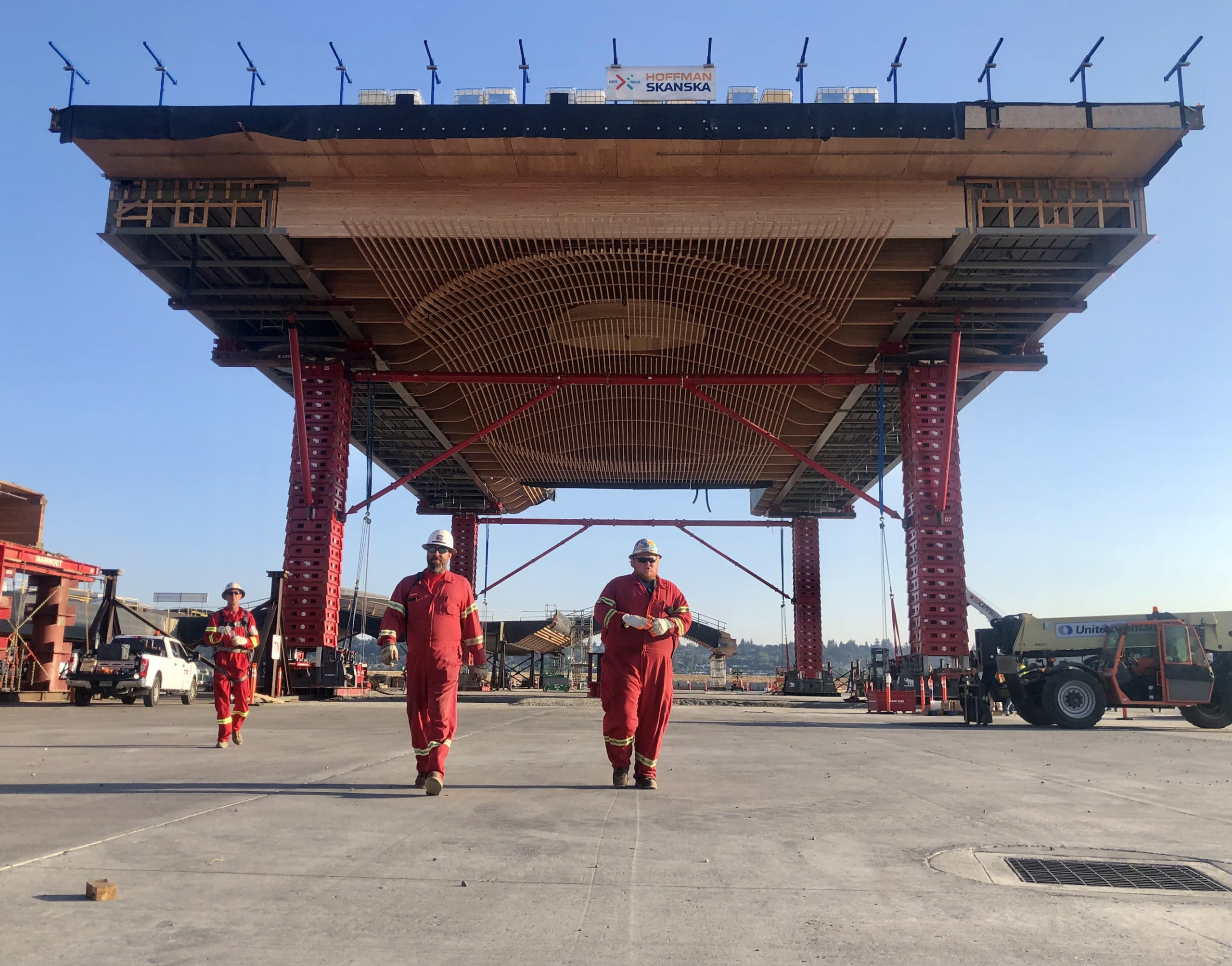
The next section was then rolled into position down the bottom flanges of the previously set section.
When the super cassette had been fixed securely, the public were allowed back into the space below.
Will it deflect?
Using wood raised concerns over deflection in the roof so, at each point in the jacking, transport, and installation process, deflection was monitored and kept within stringent criteria.
The super cassettes had steel girders in the longitudinal direction to support the 25m wooden arches and to allow the panels to be “launched” using stationary skidding equipment.
Also, said Mammoet, the supports for the launching jacks were temporary towers supported by wooden piles installed in the 1950s. To mitigate any issues, Mammoet performed extensive friction testing in its Rosharon, Texas yard prior to execution to ensure no structural damage occurred to a mockup roof panel, and that the design values presented to the client for strand jack anchoring were realistic. When executing the job on site, Mammoet monitored the loads and deflections to ensure that they were in line with the tested values.
Comments
Comments are closed.
I look forward to seeing this visually stunning roof. I always think of the fire possibilities when I visualize any wooden structure. Obviously that has been worked out but still, Portland was carved out of a forest, and they have been burning in recent years.