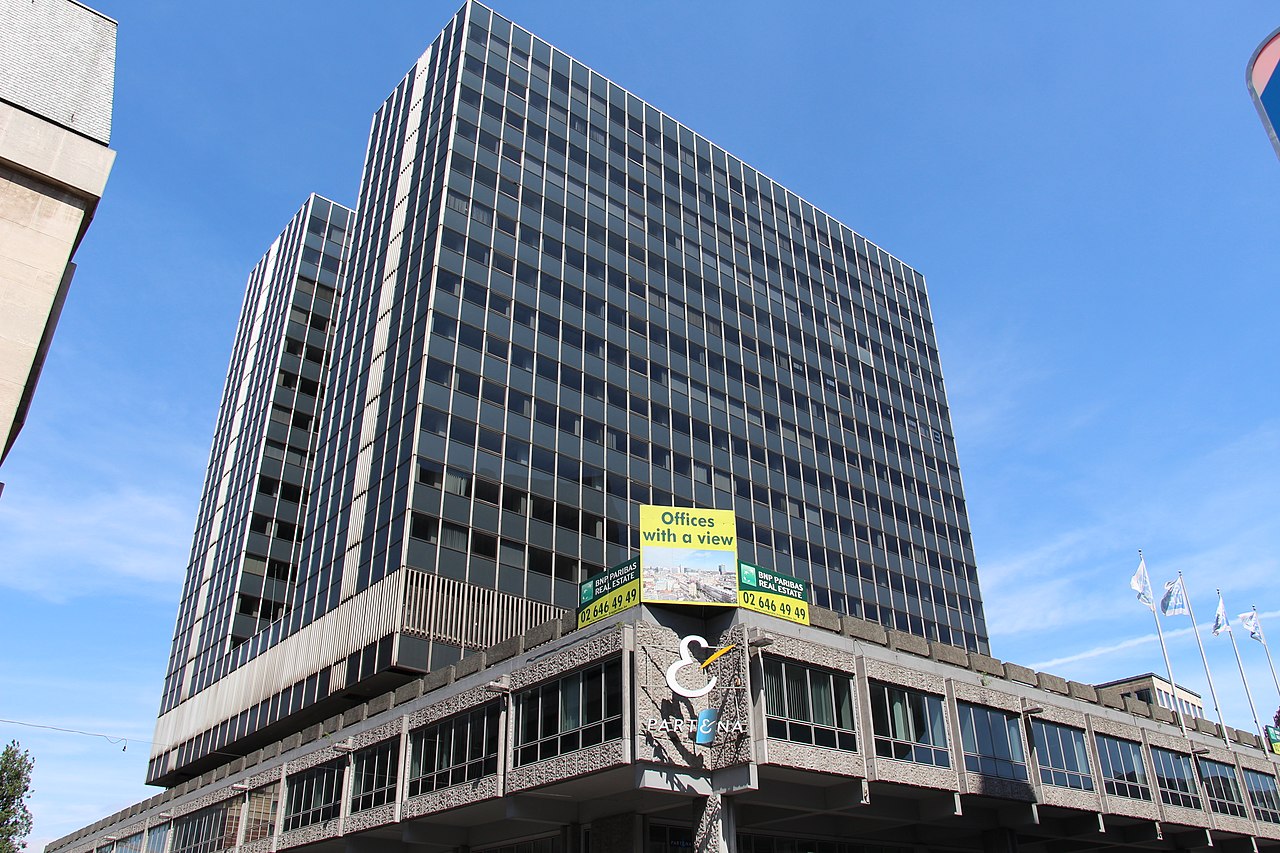
Two landmark office-tower refurbs in the Belgian capital saved thousands of tonnes of waste and emissions, and showed developers’ appetite for ‘urban mining’. GCR went to investigate
Amid the torrent of grim tidings flowing through the world’s media these days, you might be forgiven for missing the latest report on the projected rise in average global temperatures over the next 75 years or so.
It was issued by the UN Environment Programme (UNEP), a body set up to monitor states’ progress towards meeting the main aim of the 2015 Paris Agreement: limiting warming to 1.5°C.
It found that, with the policies presently in place, the actual rise might be as high as 3.1°C.
If you want to know what that would mean for life on Earth, you could look at Health Policy Watch’s website, which goes into some detail about the “cascade of catastrophes” that would likely ensue.
The point was underlined on 29 October, five days after the warning was issued, when a year’s worth of rain fell in eight hours on the city of Valencia, killing more than 200 people.
The embodied problem
According to UNEP, the buildings and construction sector accounts for 37% of global emissions. It is “by far the largest emitter of greenhouse gases”, UNEP says.
Right now, about three quarters of that 37% figure is emissions from the operation of buildings, through heating, cooling and lighting, while a quarter of it is from embodied carbon, the emissions produced in the extraction and processing of raw inputs to make building materials.
The good news is that operational emissions are forecast to shrink in the coming decades as we build more energy-efficient buildings, and as renewable energy supplies increase.
The less good news is that embodied carbon will grow as a proportion of the sector’s total emissions as more structures get built, and that won’t change unless we build less.
To demolish, or not
This issue is bound to be front and centre when, or if, governments start taking the climate threat seriously.
One option regulators may consider is forcing developers to opt for refurbishment over new build.
It’s already happening in Belgium.
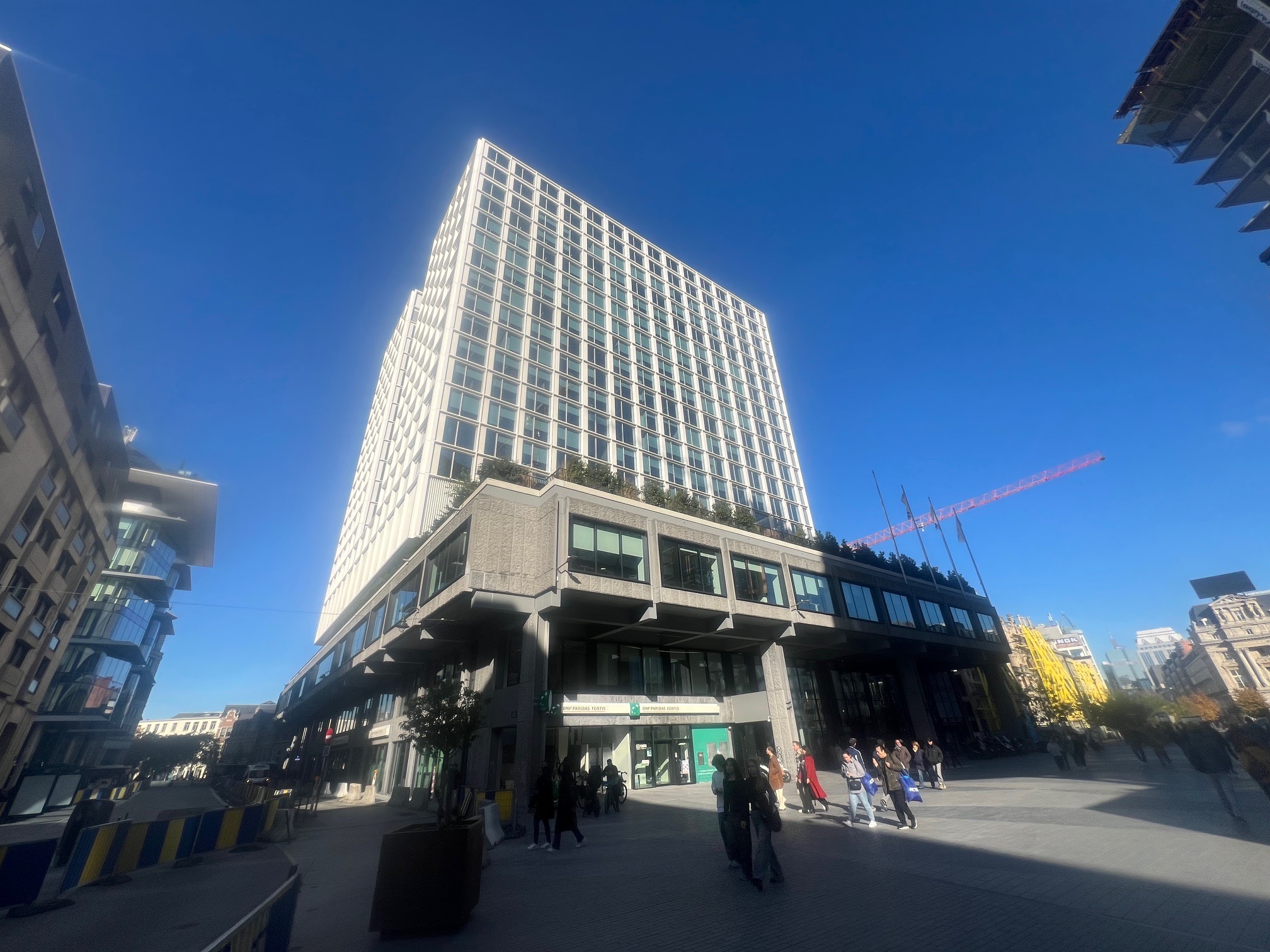
In 2019, the Brussels Capital Region forbade all demolition unless there was an “urban mining” plan to salvage and recycle the building’s elements.
Some developers are going this way voluntarily. Immobel, the country’s largest developer, has already said it will avoid new-builds.
Two pioneering projects in Brussels can help us see what has to be done to make the idea of “circular construction” – where we keep what’s already built and find ways to reuse it – a reality.
GCR went to investigate.
Circular Case study 1: Multi
The first is the former Philips Tower in de Brouckère Square in the centre of the city, a 17-storey brutalist concrete structure completed in 1969.
At that time, it fit with Le Corbusier’s modernist urban vision of free-flowing motorways lined by intimidating towers, with pedestrians confined to elevated concrete walkways.
But when the building was sold in 2016, that paradigm had fallen out of fashion.
Now the aim was to design a sustainable building that would fit in amongst newly pedestrianised streets. Could the tower be adapted to fit those requirements?
Its new owners, developers WhiteWood and Immobel, enlisted Antwerp-based architect Conix RDBM to help decide the tower’s future.
It was a fateful choice because the practice was sceptical of new-build developments.
Conix chief executive Frederik Jacobs says its founding philosophy was that it’s better for people to adapt to their environment than to try to adapt the environment to them.
Not surprisingly, the Conix team took a look at the tower and quickly concluded there was no case for demolition.
“We saw that it was perfectly possible to keep it, to adapt it, to make it a bit bigger, and there would be a good balance between the investment needed and what the building could gain in profits afterwards,” he told GCR.
One thing going for it was its solidity.
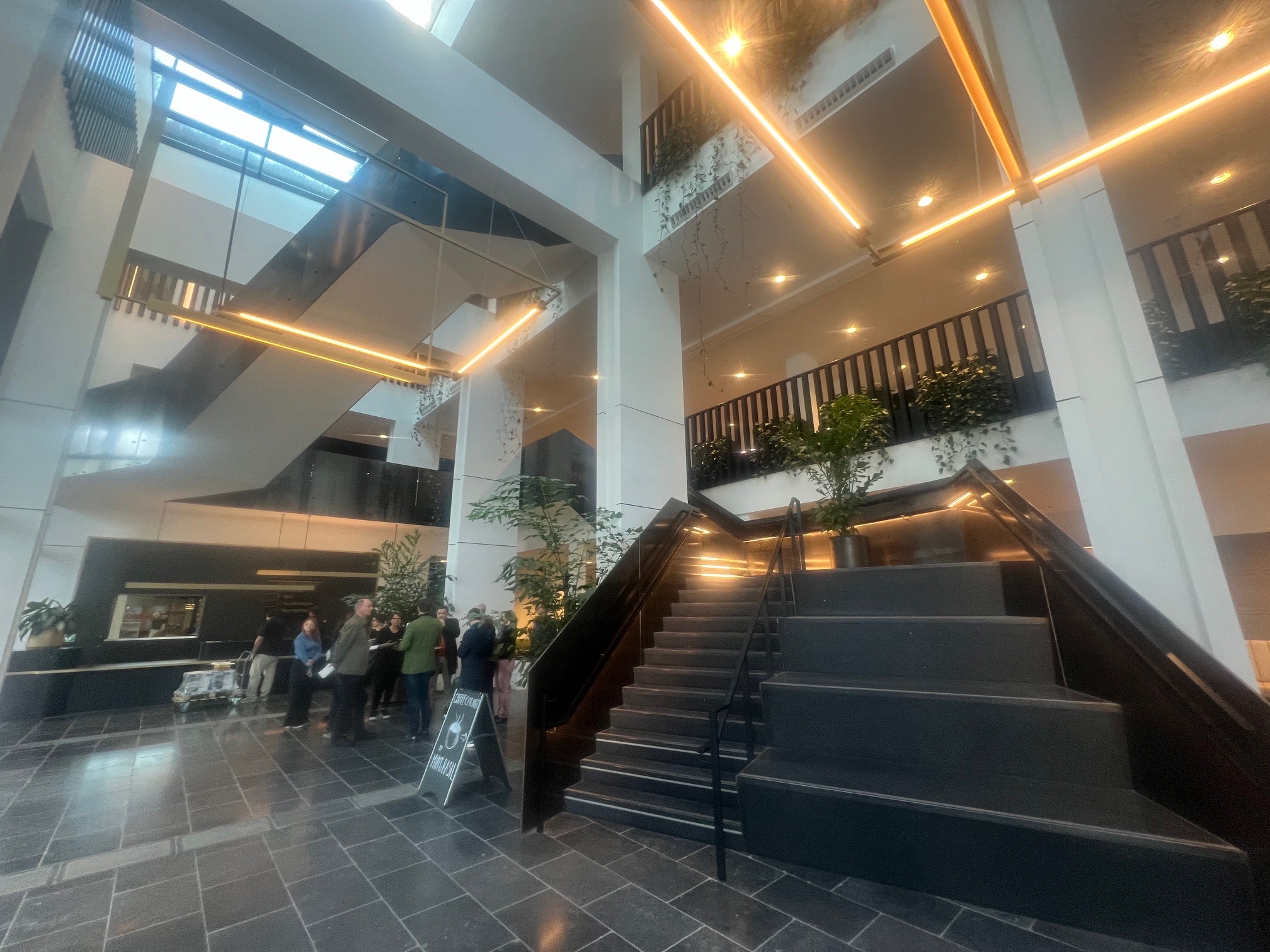
“In a sixties building like Multi, the mass of concrete is totally unexpected,” Frederik said.
“So we could use that generosity to transform the spaces, to load different functions, to add floors on the top.”
Building out and adding on
The refurb was completed in the first quarter of 2022, after 40 months of onsite work.
This saw the three-storey podium expanded by about 6m laterally and, to maintain proportional harmony, two storeys added on top of the tower.
To improve the building’s contribution to the neighbourhood, the team opened up a third-floor planted area and restaurant to the public.
Its energy performance was improved to the point that it was declared carbon neutral, a factor that helped attract its anchor tenant, TotalEnergies.
However, the really notable element was how little was changed.
A new building that is 93% old
Some 89% of the building’s materials were retained, and 3% of the new material was second-hand, much of it taken from other buildings.
Of the material that was taken away from the tower, some elements, such as the HVAC units, were reused in other buildings.
And, with an eye to future circular projects, the façade is almost entirely detachable.
Frederik said the project revealed the possibilities of circular construction for his practice, for Brussels, and the wider Belgian market.
Conix RDBM credits a company called Rotor for the idea of reusing elements of the old building in the new one.
Another company at the tip of the spear is German consultant Drees & Sommer, who also advised on the Multi scheme.
Further information on the ins and outs of the Multi project can be obtained by buying – or downloading free – the book that Conix produced on it.
Circular case study 2: ZIN
With the Multi project underway, Drees & Sommer moved on to the conversion of an even larger office block a short walk away in Brussels’ northern business district.
This was the “ZIN” project, designed by Jaspers & Eyers for developer Befimmo.
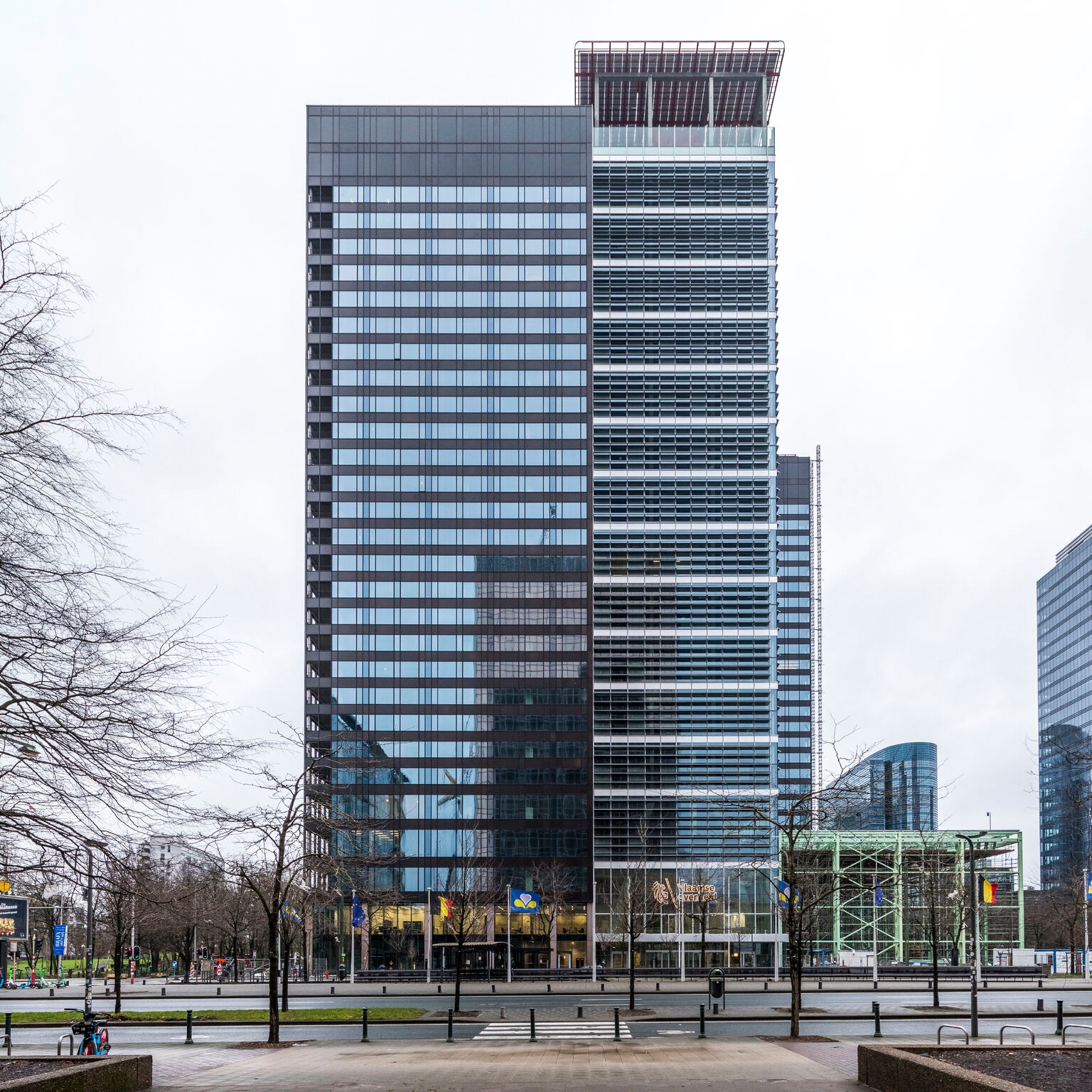
As ZIN neared compilation in the fourth quarter of this year, the results have been impressive: 95% of the mass of the existing towers were reused in some form or other.
Making a market
As inspiring as these case studies and their results are, there was nothing easy about them, as both Michael and Frederik readily admit.
They posed new challenges and required extra work, new thinking, and new skills.
Michael pointed out that recovered building elements must meet the same criteria that any new material would.
What’s its history? What’s it made of? Does it contain polyfluoroalkyl substances, the “forever chemicals” previously used freely in building materials? How much work is involved in making the item reusable?
That’s why using the wait for planning permission is important, Michael says.
“When you apply for the permit, you wait quite a long time. So, you have time to do studies, you have time to connect with contractors, with suppliers, resellers, the demolition company,” he said, noting that Drees & Sommers has a subsidiary, EPEA, that does the work needed to make used materials ready for reuse.
There is also a need for scale. Small quantities of anything are hard to use in large projects.
“You want all the same colour, all the same qualities. You don’t want to adapt the project because you have 10 different doors,” Michael said.
New skills
Frederik says a different kind of creativity is required – that and a new interest in materials science.
He says it’s relatively simple to make an inventory of what can be mined. The trick is to imagine what can be done with those elements.
“We and Rotor did a lot of experimental things with different parts,” he says. “For instance, the panels from ceilings – we tried different new coatings on them. Also, the profiles on the facade. On the one hand, we tried a lot of ways of conditioning them.
“We tried using glulam beams from industrial buildings by cutting them in parts and using them as side panels for staircases, and the lighting fixtures in the lobby are made from elements of the facades.”
From sellers to resellers
And what about the companies that make the materials in the first place? Michael points out that they, too, have a duty to be sustainable.
Circularity could confound their business model if developers and designers start treating their old materials as a new resource.
Michael notes that companies like Lindner are already targeting this market, offering sizable batches of reconditioned elements with guarantees.
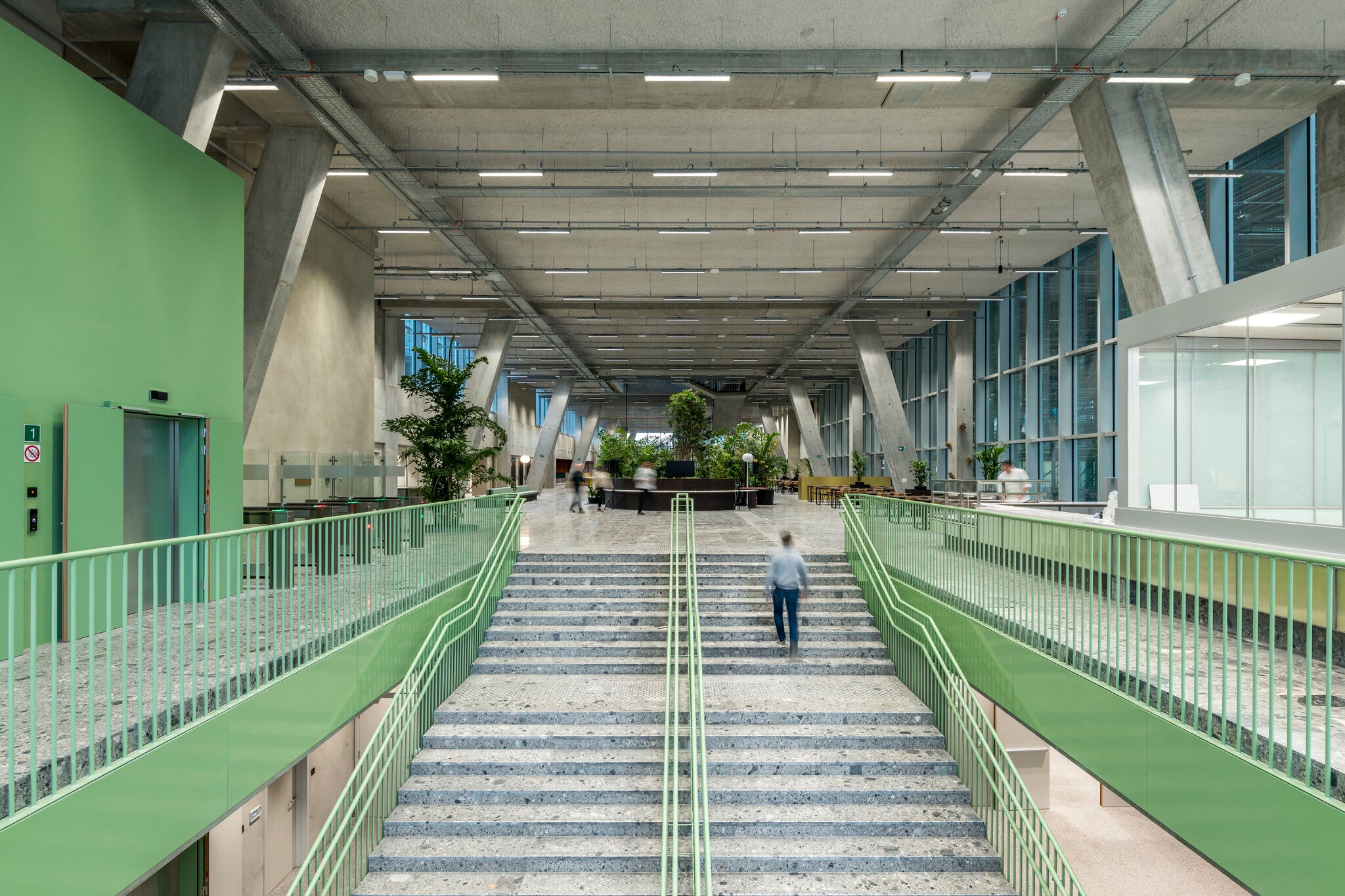
Perhaps manufacturers themselves will muscle in on the chance to sell a product more than once.
Future of circularity?
Michael is soberly realistic about the difficulties that sustainable building will face in the immediate future, given the economic difficulties the European property and construction industry is facing.
“We see now that other players in Belgium are starting to look at recycling as a complication,” he said.
“The market price of products is rising, the cost of energy is rising. So, it’s becoming more and more complicated to build. The market is asking if it is really the right way, if we see so many complications?”
He thinks the result is likely to be a slowdown in the adoption of circularity and reuse, and a need to “find solutions everywhere”.
On the other hand, the complications may diminish over time, both as the circular construction industry advances out of infancy, and as government and society recognise its importance and issue the mandates.
Then it will be for the design and build sector to price the work accordingly, and for developers to weigh their options.
Meanwhile, as that shakes out, global heating continues.
As Marcel Proust put it: to kindness and knowledge, we make promises; pain we obey.
- Subscribe here to get stories about construction around the world in your inbox three times a week
Further Reading: