The European space agency has been testing the feasibility of using 3D printing to build a lunar base on the moon. By Rod Sweet.
The operation imagined in the research involves astronauts unfolding an inflatable dome from a cylinder sent by rocket. The dome is inflated and moon soil, called regolith, is mixed with a binding agent and printed over it in layers by a robot-operated 3D printer to create a protective shell.
Leading the design is Foster + Partners, who designed a weight-bearing dome whose walls are honey-combed with hollow cells, to conserve material and to make them light and strong.
The dome must shelter four astronauts from micrometeoroids, space radiation and extreme temperatures.
The printing technology is supplied by Italian inventor Enrico Dini, one of a small number of people around the world developing 3D printing for home and building-scale construction.
His UK company Monolite supplied the D-Shape printer, which has an array of nozzles on a 6m frame that moves to spray a binding solution onto a sand-like building material. 3D ‘printouts’ are built up layer by layer.
“First, we needed to mix the simulated lunar material with magnesium oxide,” said Dini. “This turns it into ‘paper’ we can print with. Then for our structural ‘ink’ we apply a binding salt which converts material to a stone-like solid.
“Our current printer builds at a rate of around two metres per hour, while our next-generation design should attain 3.5 metres per hour, completing an entire building in a week.”
The company currently uses its printer to create sculptures and is working on artificial coral reefs.
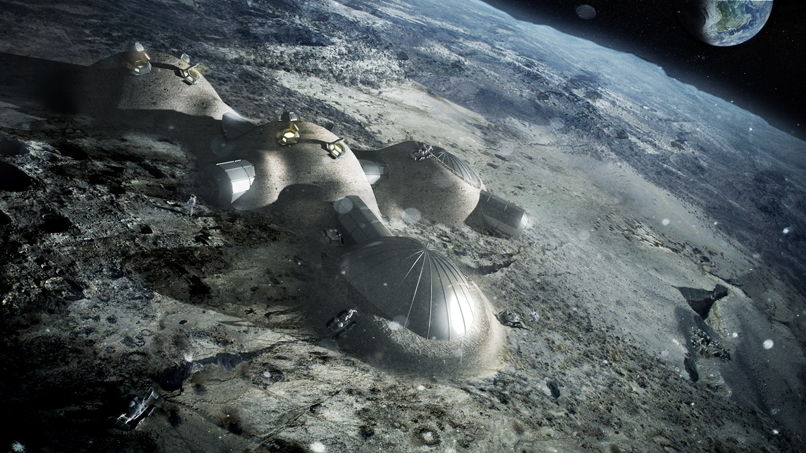
Artist’s impression of the ESA’s moon base under construction
The idea of printing the buildings arose because the soil of the moon could be used as the building material, doing away with the need to transport volumes of material from Earth.
But that threw up a problem: where were they going to find moon soil to test the technique with?
Simulated lunar regolith is produced for scientific testing by specialist companies, but it’s very expensive, typically sold by the kilogram. The team needed tonnes of it for their work.
Then Dini found some. “We discovered a European source of simulated lunar regolith,” he said. “Basaltic rock from one volcano in central Italy turns out to bear a 99.8% resemblance to lunar soil.”
The team produced a honeycombed, 1.5-tonne building block to demonstrate the dome wall.
Another problem was that the printing process relies on applying liquids, and in the vacuum of space, liquid boils away.
Project partner Alta SpA, an Italian space research firm, got busy with Pisa’s engineering university, Scuola Superiore Sant’Anna, working out how to adapt 3D printing for the Moon.
They conducted printing tests in a vacuum chamber and found that by inserting the printer nozzle a little beneath the regolith layer, small droplets were trapped by capillary forces in the soil, meaning the printing process could work.
“3D printing offers a potential means of facilitating lunar settlement with reduced logistics from Earth,” said Scott Hovland of ESA’s human spaceflight team. “The new possibilities this work open up can then be considered by international space agencies as part of the current development of a common exploration strategy.”
In fact, NASA beat the ESA to the idea. In 2011 NASA awarded a research grant to one of the other pioneers of printed buildings, Prof. Behrokh Khoshnevis, at the University of Southern California, to develop potential lunar structures as part of the NASA Innovative Advanced Concepts programme. Khoshnevis received a second grant last year to continue the research.
Meanwhile, back in Europe, other factors to study include controlling lunar dust, which is hazardous to breathe in, and how the printer will work in extreme temperatures. 3D printing works best at room temperature but on the Moon temperatures vary enormously, with days and nights lasting two weeks each.
So the best site for the base may be at the moon’s southern pole, where there is near perpetual sunlight.
“It has been a fascinating and unique design process, which has been driven by the possibilities inherent in the material,” said Foster + Partners’ Xavier De Kestelier, partner in the firm’s specialist modelling group.