Caterpillar Inc, the world’s largest maker of construction machinery, has announced that it will invest in Hadrian, a brick-laying robot developed back in 2015 by an Australian aeronautic engineer.
The deal sees Caterpillar lend its weight to developing the technology, which can now lay 1,000 bricks an hour.
The US company will buy $2m of Fastbrick Robotics shares over the next year with the option to make a further $8m investment later, subject to the approval of Fastbrick’s shareholders. This money will be spent on further research into the technology, the development of a commercial product, together with sales and servicing. Â
The two companies will also form a “strategic alliance board” to oversee the development of the system.
Hadrian was invented by Mike Pivac, who developed the idea in 2005 during a shortage of bricklayers in Perth, Western Australia. He then spent 10 years developing a 28ft-long prototype.
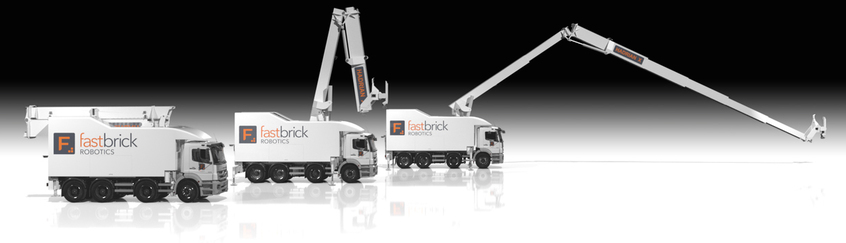
The Fastbrick system (Fastbrick)
Commenting on Caterpillar’s investment, Pivac said, “Fastbrick Robotics is delighted to sign a memorandum of understanding with Caterpillar and welcomes the company as a new shareholder.
“Caterpillar is a globally recognised industry leader, and we look forward to collaborating with the company and uniting our teams to share ideas, pursue innovation and explore opportunities to commercialise our unique technology.”
The latest iteration of the technology is Hadrian X. This can lay 1,000 bricks an hour. The 98ft arm, which is controlled by a CAD program, is able to cut and lay bricks in a precise pattern, and to inject mortar to cement them in place using in inbuilt nozzle. The boom auto-corrects 1,000 times a second to ensure that it is putting the bricks where they are meant to go.
Fastbrick’s promotional video of the system in action can be seen here.
The company’s share price rose 24% after the tie-in with Caterpillar was announced. The initial $2m purchase was made at 10 cents a share; if the $8m placement goes ahead, it will be at 20 cents a share.
Top image: Hadrian in action (GCR)
Further Reading:
Comments
Comments are closed.
Well that will make a lot of bricklayer’s really happy
Amazing,I have been on site for 30 years,I need joint replacement in my elbows and thumb,my back aches all the time and my knees are shot.what took you so long guys?
will not replace a skilled mason!
This is another example of a misguided approach to automation. Sure, it’s cool to lay bricks with a giant arm, but the actual portage and placement of bricks is only one small aspect of building any brick structure. The design of structures are heavily interlaced with dozens of other construction elements which must be attended to in concert with wall building. I see similar mistakes made all the time in people’s approach to automation in manufacturing. In this market, it makes much more sense to put the automation in a factory and pre-fab modular walls or structures off-site where you can control conditions and maintain/operate complex systems. Simulations and factory demos are easy when compared to full scale systems “in the wild”. Not to be a buzzkill, but this won’t be a practical success. Do some DFM/DFA and change the approach and product.
I cant see it working on a UK building site with the inclement weather and the various changes in weather during a normal shift pattern. Plus the bricks in the UK are not the best in measurement