Developers in Kenya have begun building houses from polystyrene to offer residents better protection from the hot sub-Saharan sun.
The unusual construction technology is gaining a foothold in Kenya’s fast-expanding housing sector, according to Reuters, with experts saying the approach is cool, cheap and environmentally friendly.
Panels for putting homes together are made from a light cellular plastic foam, a by-product of oil refining, which consists of mini spherical particles containing about 98% air.
The foam is sandwiched between steel wire mesh and, once the panels have been joined together, they are sprayed with cement to support and strengthen the walls.
In one new development, around 50 polystyrene houses have been built in Kajiado County, southeast of Nairobi, Reuters reports.
“Its temperature remains constant, even in extreme weather, unlike the houses I have lived in before,” one of the development’s residents, Justus Opiyo, told Reuters of his new house.
At another location, in Ole Kasasi, a five-storey apartment building with 20 flats is going up, according to Reuters. They are among a raft of polystyrene construction projects started in Kenya by different companies, including the Malaysian firm, Koto Corp.
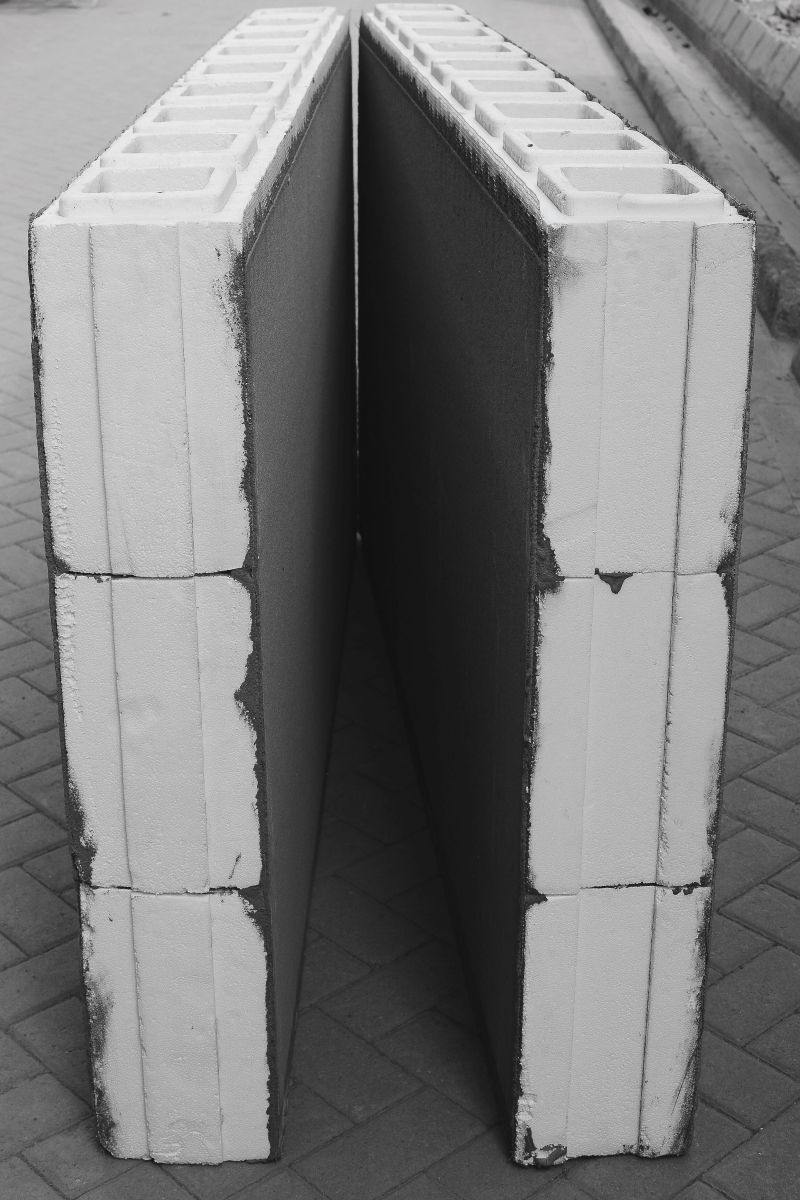
A Koto polystyrene wall panel come in sizes of 1.2m 1.8m in length, with thicknesses up to 200mm (Koto)
Because air is a poor conductor of heat, polystyrene houses can offer better insulation than homes made from timber or concrete.
Romanus Otieno, an urban planning lecturer at the University of Nairobi, told Reuters that polystyrene is ecologically friendly because it uses very little water. That, he said, outweighs the negative side of polystyrene being derived from crude oil, especially in arid regions.
Otieno said a standard two-bedroom polystyrene house costs about $6,700, while one made of bricks can cost twice as much. The difference is mainly due to lower labour costs, as polystyrene is easier to move around and put in place, he noted.
He added that polystyrene homes are also quicker to build, which could help reduce housing deficits faster.
An architect in Kenya, Dennis Muli, of Gem Archplans in Nairobi, told Reuters that the lightness of polystyrene meant less timber is needed to support the building, which could help reduce deforestation.
Muli insisted that polystyrene homes could be just as durable as concrete ones if the correct procedures are followed during construction, and urged government and non-profit organisations to advocate polystyrene use because it is cost-effective and relatively green.
However, university lecturer Otieno said the cost of polystyrene building needs to come down if it is to really take off in Kenya. Panels now cost $21 per square metre, but the price should be halved to entice more home owners and developers, he said.
Top image: A recent handover of a Koto polystyrene house in Chuka, Kenya (Koto)
Comments
Comments are closed.
It is similar to Insulated Concrete Formwork which is an accepted method of construction in UK using eps. The difference is that the concrete filling is apparently not needed for a single storey with a similar lightweight roof. The render coat does seem very thin though for fire protection and strength.
It is still expensive so I would rather go for the proven and tasted brick and stone houses..
What are the fire risk implications here?
From the photograph noted, are the vertical voids in the panels filled with concrete to aid stability ? And how are the panels joined together ? Surely there must also be some weight factor involved to combat wind conditions ?
I’d be very interested to see how this works and whether this system meets UK Building regulations.
What a fantastic idea, houses with walls made entirely out of expanded polystyrene – cheap, warm and quick to build. Now why didn’t someone think of this before…oh yeah BECAUSE THESE ARE DEATH TRAPS. EPS is an inherently combustible thermoplastic insulation material which will emit noxious fumes in the event of ignition – not to mention collapse of the structure once the EPS starts to soften under the developing fire. I’m all for cheap innovative buildings but they need to be technically sound and not at the expense of occupant safety…unbelievable – even more so that the CIOB have published this article without even mentioning the ‘elephant in the room’.
Are there any problems with termite or rodent attack?
$21 per square meter to me is quite pricey. Even when you save on time and Fundi labor, you lose on cost per piece of panel.
The negativity in the posts is astounding. I certainly see the merits. The basic concept seems similar to the the ICF blocks which is an increasingly popular home build option which meets with existing fire regulations. I’m sure the panels forming the walls are not capable of high imposed loads vertically but then there is surely some main support elements included for the likes of the roof support and for rigid support of the frame etc.
I agree with the comments questioning the fire resistance of this type of construction. In particular the noxious fumes and the rapid collapse of the polystyrene derived structure in the event of fire, is just too obvious. Adam’s views are typical of someone who doesn’t know (or care) about the consequences of such unresolved fire hazards. Straw bales with steel mesh and spray-on concrete coating would have better stability in the event of fire – and you won’t find any 3 or 4 storey apartments constructed with the latter!
We do not need crude oil to produce EPS. https://www.youtube.com/watch?v=86VhcYIQjOI
I seen that this is ICF panel , produce by shape moulding. Also, I curious about your building system. Do you use iron and cement inside of ICF hollows ?
Fire proof polystyrene ,mad in Africa ,exported to Europe???
people do talk some rubbish, it is possible to fully fire proof eps, there is a flame retardant added I have seen tests it will not burn. With concrete on ether side and non exposed anyway how would it catch light in the first place, there isn’t any eps exposed. Eps is widely used for external insulation of houses in the UK with a render on top this is no different, there is a cover over the eps how is it going to catch light, also flame retardant for such applications. please before criticising please get better informed.
Green? What about recycling?
I think its good but can only try it for partitioning the rooms.how strong is it on perimeter wall.some of us have cattles that may lean or rub their hides on it.will the wall be strong enough to stand that???
I agree with Andrew Marshall about the reduced risk of fire because the fire prone material is covered and so chances of ignition are minimal…unless you are working very hard to burn the stuff to prove it doesn’t work! My concern would be electrical fires as conduits pass seem to pass right through the material…ave seen 2 types of these panels and one seems to reduce risk in that the conduits would be covered by concrete rendering them less of a fire hazard…I think the price isn’t justified! I believe the Chinese can make this price reduce by a factor of four! The challenge to whoever is making this stuff is to watch out before the Chinese take note of the demand and they attack your territory!…finally, you look at this stuff and you have lived or seen low income housing (which is what this stuff is meant for and you wonder; what is more fire prone; a timber house (which dries with age) or this stuff?) some people are just made to live to promote poverty especially to third world countries! Kenyans; these “fire crusaders” will find loopholes!…next You will hear such a house is carcinogenic!…do a cost/benefit analysis and take your decision and forget about prophets of doom!
I have worked with polystyrene walls for over 15 years and one big drawback is they are easily attacked by rats, who easily bore holes and eat the walls. otherwise it makes very good insulation against heat. Its still not as cheap as other available materials like mud bricks.
A moladi cast insitu wall cost in South Africa is $8 per square meter – A solid reinforced wall – #1 criteria for the homeowner is “social acceptance” in other words the knock test
There is another ‘elephant in the room’ that nobody wants to talk about. That would be durability of houses built with EPS panels. I wonder how long these structures would last compared to a conventional brick and mortar house? Why don’t developers want to raise more awareness about that?
I’m considering using this technology but could someone please how durable the houses built from this technology are?
This technology has been around for a while now. However, it seems to be a lot less popular than expected given that it’s proponents say it is about 30% more cost effective than the conventional building materials. What could have caused the slow uptake?