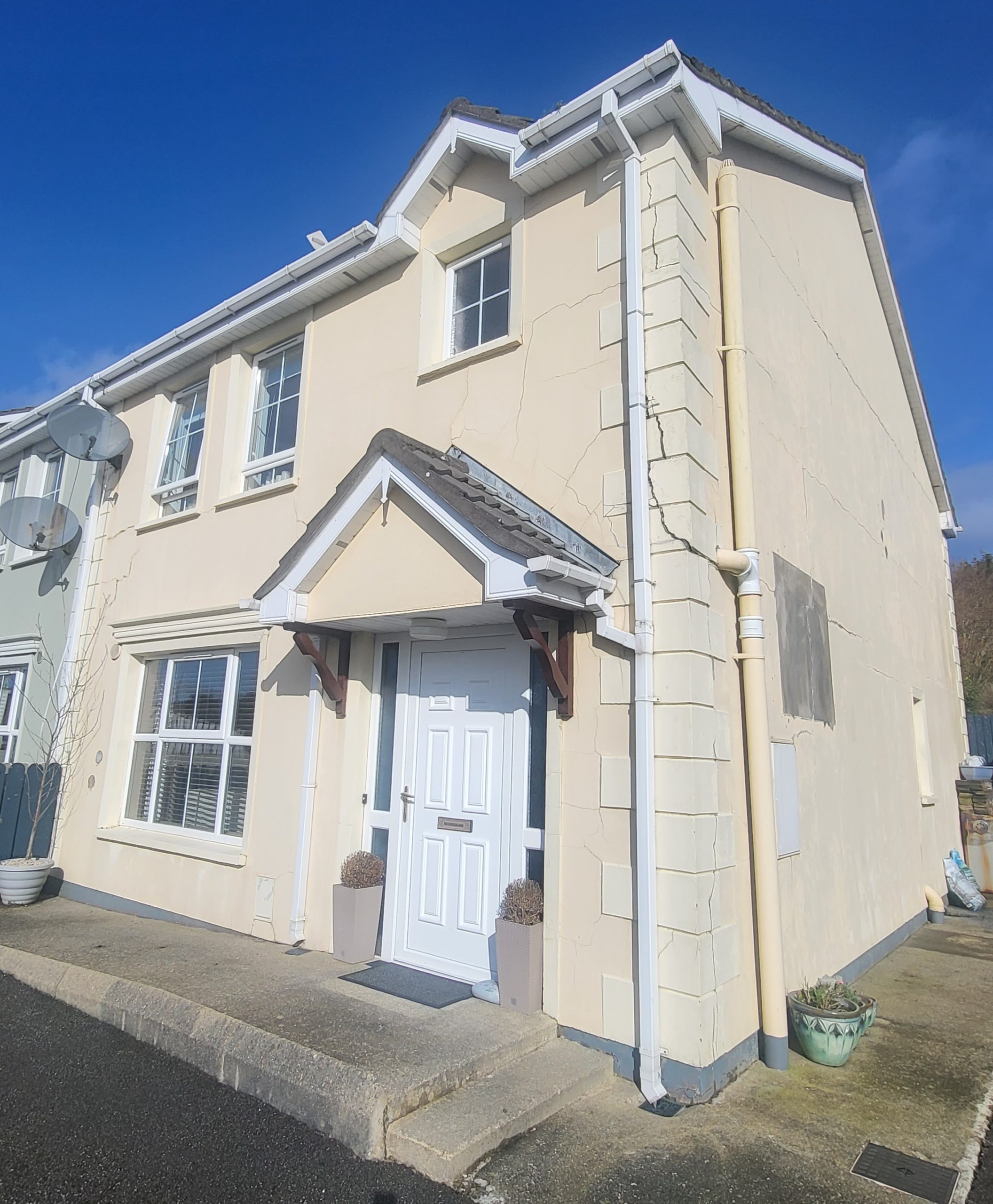
Thousands of homes in Ireland are crumbling. In videos posted online, angry and despairing owners pull rotten concrete blocks from their walls and dash them to dust on the ground.
An estimated 7,500 homes, concentrated in but not restricted to the northwestern county of Donegal, have been affected by the so-called “Mica Crisis”, in which homes built largely from the late 1990s and into the 2000s have too much of the mineral, muscovite mica, present in the aggregate of their concrete blocks, according to one theory.
Mica absorbs and stores water, which expands when it freezes, thus undermining the cohesion of the cement and weakening the block. Deterioration is progressive because each freeze-thaw cycle opens the block to more water ingress. Cracks appear in walls, deepen, and spread as the blocks give way, allowing more water ingress.
Another impurity in concrete blocks, pyrite, is causing similar problems in western counties like Mayo, Galway, and Clare.
A third impurity – pyrrhotite, an iron sulfide that oxidises on contact with water and oxygen, creating new compounds that expand – was put forward by researchers from Ulster University and elsewhere last year as an overlooked, contributing factor in the mica crisis.
It’s political now
There’s no easy fix. Each affected wall must be replaced. In some cases, the whole house must be demolished and rebuilt.
The problem became apparent in 2013, but it wasn’t until June 2020 that the Irish government introduced an assistance scheme, offering 90% compensation, with grants of €49,500 for external wall replacement, rising to an upper limit of €247,500 for complete demolition and rebuild.
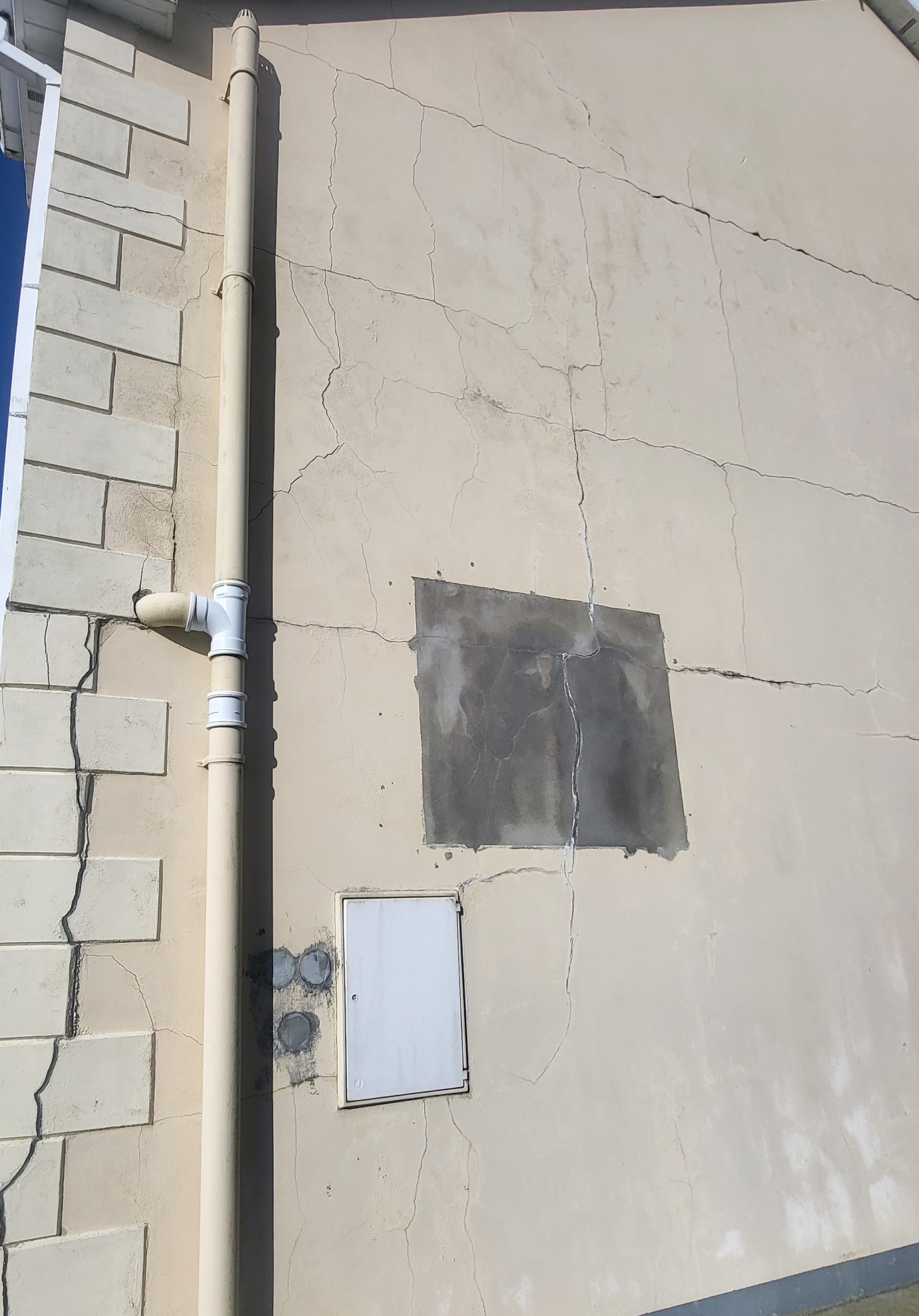
It was widely denounced as inadequate, since homeowners had to pay €5,000 for a mica test and, in many cases, the cost of demolition and rebuilding would far exceed €247,500.
Thousands marched in protest in Dublin in June and October 2021.
In November that year, the government upgraded its Defective Concrete Blocks Grant Scheme, offering 100% compensation for mica and pyrite problems, with the upper limit for full demolition and rebuild increased to €420,000.
Many are still not happy since, in some cases, the full cost of demolishing and rebuilding is greater than €420,000.
The enhanced grant scheme was originally costed at €2.2bn but, in 2022, cabinet ministers were warned that the cost of the scheme could surpass €3.6bn.
Last year, affected homeowners formed the “100% Redress” party calling for, among other things, no cap on the grant, a public inquiry into how regulations failed to stop the sale of defective blocks, and the prosecution of those responsible.
In June this year, the party won four seats on Donegal County Council.
The pyrrhotite hypothesis could complicate things further. Researchers argued that remediated houses will just keep crumbling if blocks containing pyrrhotite are left in place, and that the government’s remediation grant scheme will fail if pyrrhotite is not taken into account.
One of the paper’s co-authors, Paul Dunlop, is a professor and research director at Ulster University’s School of Geography and Environmental Sciences, and owns a home with defective concrete.
Aidan O’Connell is a chartered engineer, an expert contributor to the National Standards Authority of Ireland (NSAI), and a veteran of countless pyrite remediations.
He urges caution.
“It has not really finalised, and the NSAI committee that I’m a member of are meeting still at the moment [to review] all of the most recent analytical data and test data that we have in relation to the chemical analysis of the samples that are coming in,” he told GCR.
How could this happen?
It’s not entirely clear yet.
In 2017, a government-convened expert panel published a report referring to “vulnerabilities in the building control system” exposed by the 2008 economic crash.
Aidan O’Connell puts it more strongly.
“There was no building control inspections by local authorities in Ireland back in 2017,” he said.
“It just didn’t exist. They may have carried out inspections on infrastructure they were in charge of, like roads, drainage, and pumping stations, but they were relying on the building industry as a whole to self-certify and to manage the process (according to) the guidelines,” he said.
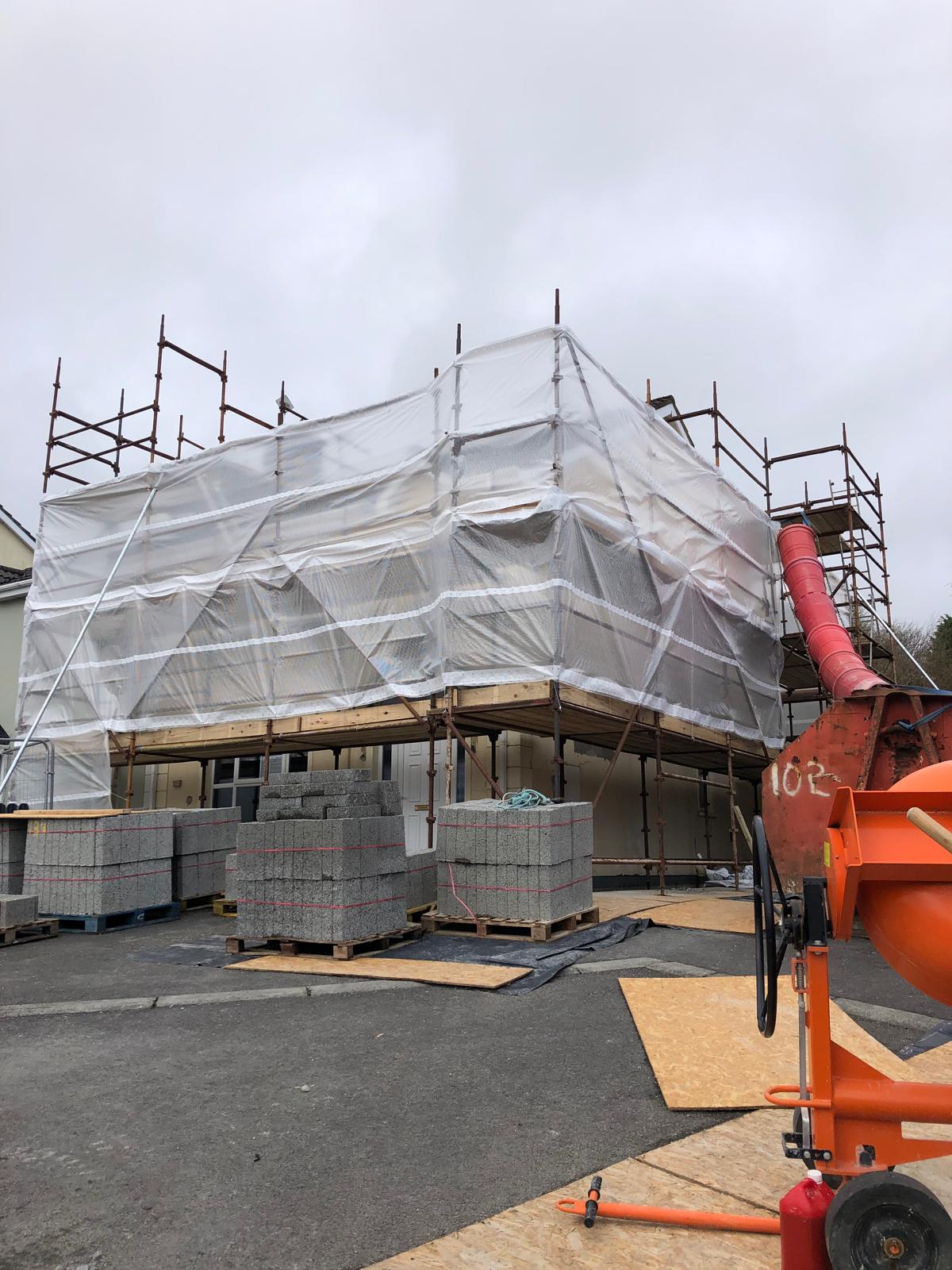
O’Connell, who knows many block manufacturers, ventures that they were not “aware of how big a problem was going to happen down the road”.
“I really genuinely don’t believe that any supplier would have readily sold a product with full knowledge that this was what was going to happen,” he said. “No one is that stupid.”
A major supplier of concrete blocks in Donegal was Cassidy Bros. In public statements reported by The Irish Times, the company has said it always adhered rigidly to building standards, and did tests at its on-site laboratory that were independently audited. It was, it has stated, “as shocked as everyone else when damage emerged in properties”.
In November 2022, The Irish Examiner reported that 1,100 legal cases had been launched, with more expected.
On 25 July this year, the European Commission launched an infringement procedure against Ireland for “not carrying out market surveillance as required” by the Construction Products Regulation 305/2011, which requires authorities to monitor the manufacturing and sale of construction products before they are used.
Noting the “very serious damage” to thousands of properties, the Commission said the Irish authorities “limited their monitoring activities to finished buildings or finalised civil engineering projects. The limitation of market surveillance activities to on-site measures endangers the free circulation of safe construction products in the Union.”
The Commission gave Ireland two months to “respond and address the shortcomings raised”.
Why did it happen when it did?
Aidan O’Connell believes the pyrite and mica crises revealed themselves when they did because of geography and weather.
The affected counties are on the west coast, where buildings are battered by rain driven by strong westerly and southwesterly winds off the Atlantic.
Then came the “Big Freeze” of 2010, when temperatures plummeted over November and December.
It got especially bitter in the latter half of December, which saw nine consecutive days when temperatures remained below zero in some areas, with night-time temperatures regularly below -10°C and reaching as low as -17.5°C in County Mayo on Christmas Day.
County Donegal saw its most extreme snowfall since 1984.
That freeze, says O’Connell, probably got the ball rolling, with bigger cracks opening up and starting the process of progressive deterioration.
Fear and despair
One firm squaring up to the crisis is Anamore, a building remediation specialist based in Omagh, County Tyrone in Northern Ireland.
Its co-founder and director James McCallan says only around 230 remediations in the affected counties have been done so far, but that applications for grant funding have picked up “massively” in the last seven months.
He believes one reason for the sluggish uptake has been fear and despair among those affected.
“Your child’s lying in their bed, you’re lying in your bed wondering, is this house safe? It’s that fear that weighs so many homeowners down, psychologically, over many months and years.”
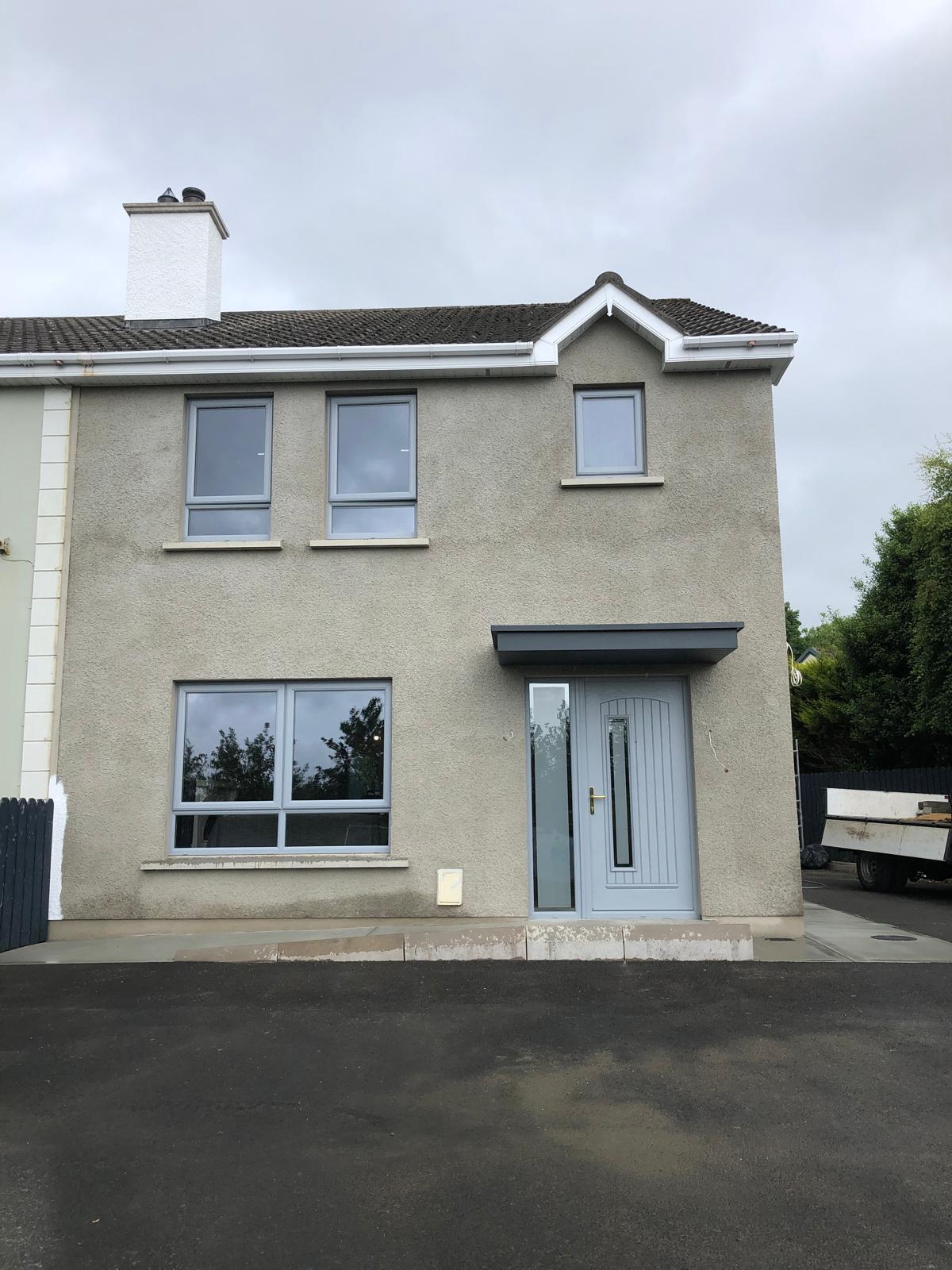
The problem is so big and frightening, he said, that people don’t know where to start.
“Sometimes,” said McCallan, “they just put it off, going ‘Do you know what? With the stress levels, I’m just going to leave this for six months until I have the energy to find who it is that I need to find, or figure out where I need to go.’
“And then it’s just left until it gets to a point where the house falls into a state of complete disrepair. And then it’s desperation.”
Doing the doable
Not all affected properties need complete demolition, and many remediations can be done within the €420,000 limit. McCallan said none of Anamore’s mica remediations so far have exceeded that limit.
He believes education and outreach are needed, which is why he gave tours at a successful project in Letterkenny, Donegal, and publicised it in local media.
There, the end-of-terrace house needed only its outer block wall replacing in a five-month project.
In standard construction, walls consists of a 100mm-wide outer block-layer, a 100mm-to-150mm-wide cavity, and a 100mm-wide internal block-layer.
After long exposure to high winds and driving rain, water can seep into a wall’s outer and inner layers, but that wasn’t the case in Letterkenny, where only the outer wall was seriously affected. Cracks in the inner wall were carefully repaired.
The new outer wall was constructed using 13N concrete blocks, tested for pyrite and mica, above damp proof course level.
In most cases builders apply one scratch coat, followed by the finish coat. In Letterkenny, the house was built with a smooth render finish, but Anamore insists on two scratch coats. It further strongly recommends a wet pebble dash as the finish because it’s more impermeable.
Then the rebuilt walls must be left to cure for at least two months before painting.
“If you’re going to do something, do it once and do it right,” McCallan said, “it’s our job, our duty, to leave something better than how we found it.”
McCallan said this kind of remediation requires specialist knowledge and experience that most general building contractors may not have.
Combatting the fear factor
“We need to show it and let people see what needs to be done and what can be done,” he said, “and to help people understand that there is a support network out there.”
“Look at it like this,” he added. “You and I live in a development. You work in finance, I work in construction. I’ve an idea what’s wrong, you don’t.
“But then you see my property being remediated. You and I talk. You go ‘So this is what I do? Okay, now I’m armed with much more information’. Then the homeowner next to you sees, and it’s like a domino effect.”
McCallan said he expects mica remediation work to increase from about 5% of Anamore’s business now to 30% in the coming years.
The company has set up the Anamore Academy to give college students hands-on experience in “all things building remediation”, from replacement of unsafe cladding, balcony remediation and internal fire compliance to pyrite and mica.
Clarification and update: Ireland’s defective block crisis
In response to reader feedback on this article, we wish to make the following clarifications and updates.
First, as the article notes, recent research suggests that the presence of iron sulphides – predominantly pyrrhotite – in the affected blocks may be an overlooked cause of the blocks’ degradation. We further clarify that some researchers involved maintain that this finding refutes the mica freeze-thaw hypothesis the article also outlines.
Further to that, we understand that the National Standards Authority of Ireland (NSAI) is considering research on internal sulphides attack in its current review of Irish Standard 465:2018, which addresses the assessment, testing, and categorisation of damaged buildings incorporating concrete blocks containing deleterious materials.
Finally, we understand that NSAI, one of whose expert contributors offered commentary for the article, is a defendant in a case in Ireland seeking damages on behalf of affected homeowners.
- Subscribe here to get stories about construction around the world in your inbox three times a week
Further reading: