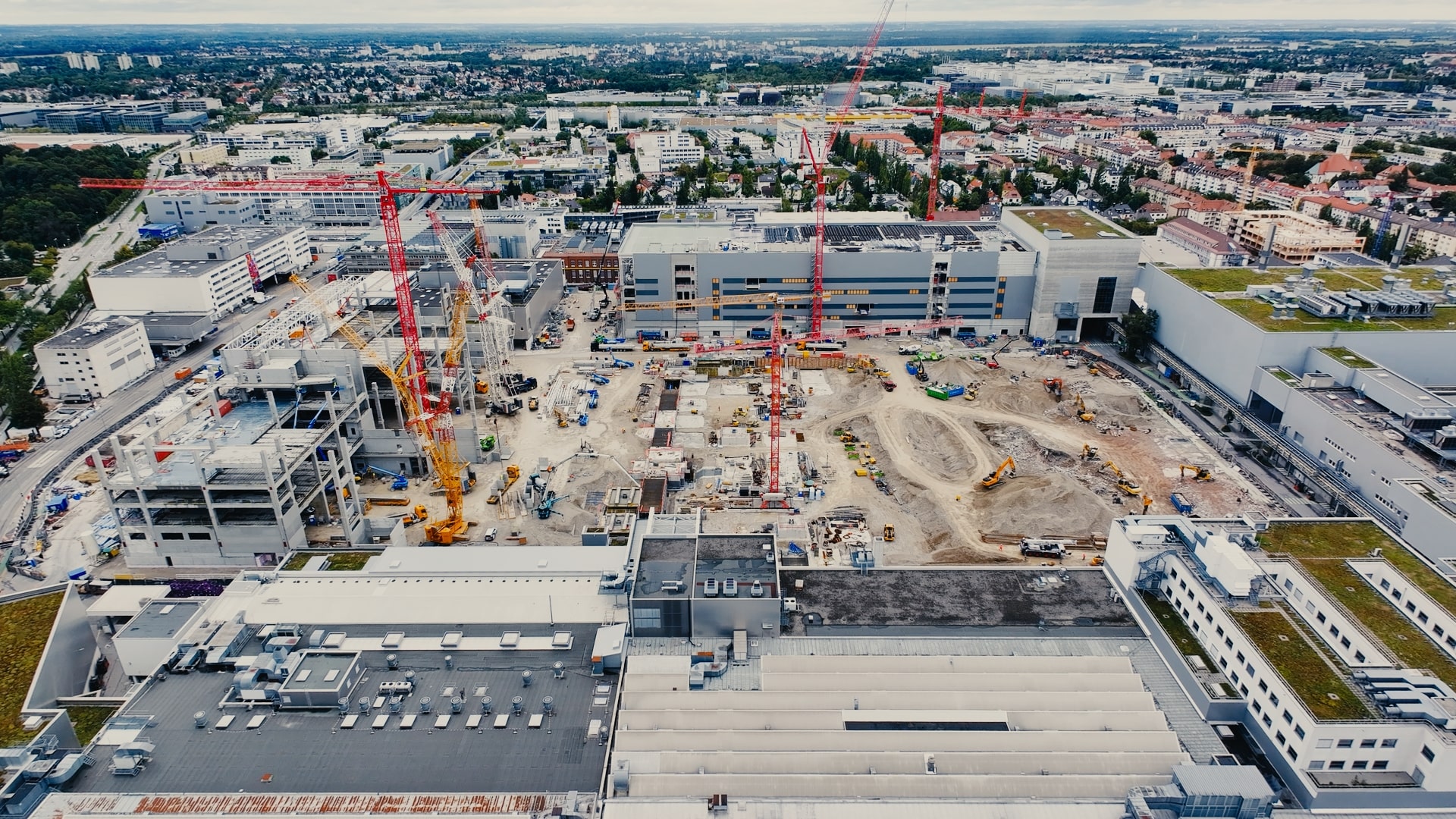
German consultant Drees & Sommer has described how it is steering a €650m conversion of BMW’s main factory in Munich to prepare it for producing cars with electric-only drive systems from 2026.
It is using a form of partnering as well as “lean” construction principles and a digital twin to deliver new production halls without disrupting operations at the site, where nearly 7,000 employees produce a thousand vehicles a day.
Drees & Sommer is working with German contractor and engineer Porr on the project.
“The biggest construction challenge is the tight schedule,” said Drees & Sommer’s senior team head, Maximilian Lammel
“We started the demolition work in April 2023 – the new vehicles must roll off the production line in November 2026. During this period, the construction work must not interfere with ongoing vehicle production. For this to work, an efficient construction workflow is crucial.”
Partnering
The project uses a delivery method known as “general contracting in partnering” in which the client, project manager, and construction firm interact as partners in all phases.
“Mutual and joint responsibility improves the communication between stakeholders and enhances the quality of construction projects,“ says Maximilian Lammel.
“In conventional delivery methods there are many sub-areas of responsibility, with communication being conducted via several interfaces. This often leads to misunderstandings and hampers the flow of information, especially in large-scale projects. The consequences could be disastrous.”
Lean construction
The team is applying “lean” production principles borrowed from the automotive industry itself.
One lean principle is the precise timing of each step in production. If timing slips, supervisors find and fix the fault right away.
“On a conventional building site, on the other hand, defects often go unnoticed for a long time – sometimes so long that, at some point, all work comes to a standstill,” Drees & Sommer noted.
The company’s automotive division head Florian Langlotz said the project’s programme was developed “in as much detail as necessary, so that all trades work together to the best possible effect”.
That led to a clear definition of which employees, machines, materials were needed at a given place and time.
Digital twin
“To avoid any nasty surprises on the building site, we use virtual planning,” said Drees & Sommer’s senior team head Simon Rogalski.
“Each building is initially planned in the form of a digital twin, which brings together all the relevant data. In this method, the construction planners not only describe the geometry of the new halls. The model can be enhanced with different kinds of data on the materials used, their cost and service life, as well as sound insulation and fire safety properties.”
All parties in the project use the same model, so any conflict in the model shows up right away.
“Errors are not left unnoticed until the construction process, where they would then lead to expensive delays,” the company said.
This level of planning does increase the planning effort at the start, but pays off over the course of the project, it added.
- Subscribe here to get stories about construction around the world in your inbox three times a week