Engineers in New Zealand are praising geological 3D modelling software for helping them design a major motorway through complex topographical conditions.
They say the software lets geologists create a visual model themselves without the help of a CAD technician, which made the process quicker and facilitated better communication between designers and contractors.
It also allowed them to pick the most cost-effective route through the hilly terrain because they could compare the cut-and-fill quantities required as the alignment varied through different slope profiles.
The motorway, costing an estimated NZ$700m, is the 18-km PÅ«hoi to Warkworth extension, north of Auckland. With Auckland’s population growing, the Warkworth region is classed as a growth centre and the number of cars travelling the route daily is set to rise from 19,700 in 2012 to 31,300 in 2026.
The road will cut through steep hills and valleys, requiring seven bridges. Seven million cubic metres of earth must be moved amid the presence of soft alluvial sediments.
The design work was subcontracted to Design Joint Venture (DJV), comprising engineering consultants Beca and Tonkin + Taylor, who used Seequent’s Leapfrog Works 3D geological modelling software.
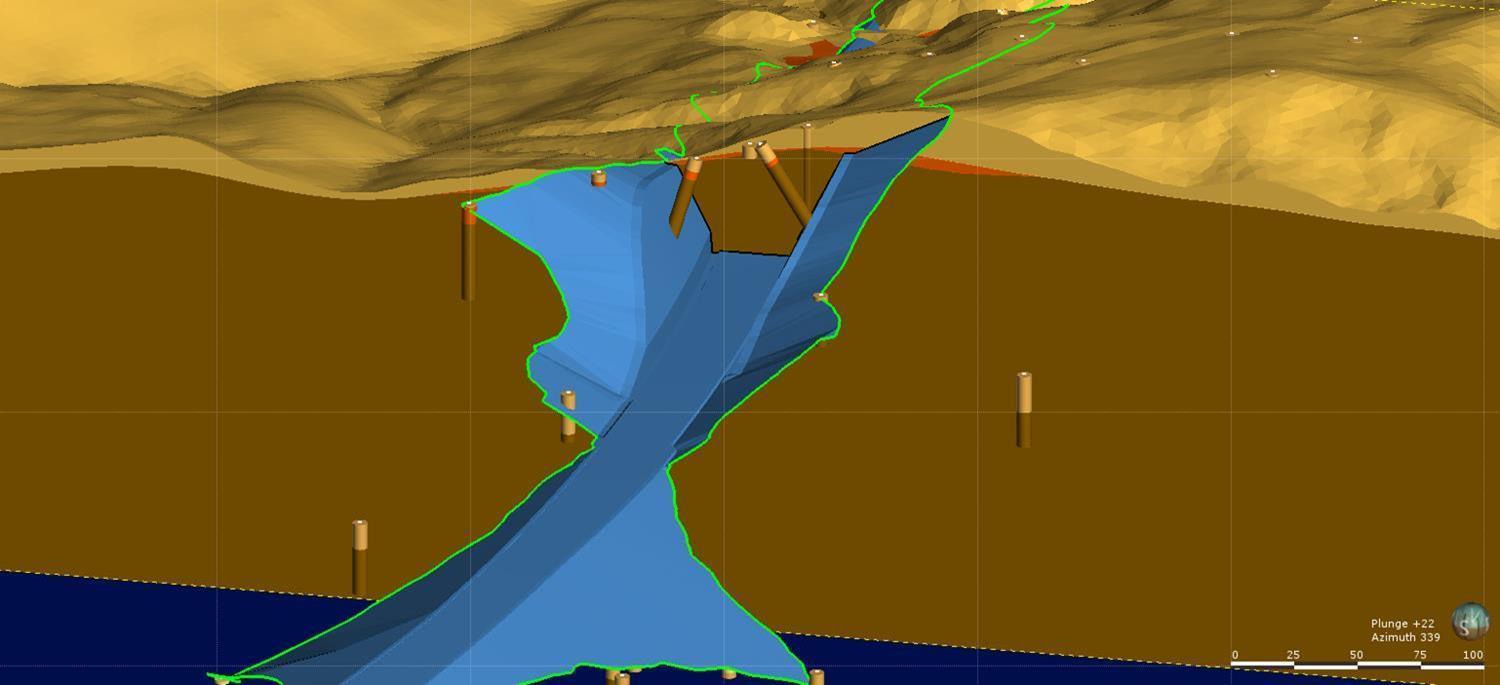
Cut and fill requirements vary widely depending on topography (Seequent)
“It was important we could use a modelling tool that worked flexibly around the different geology and surface types to give accurate outputs,” said Chris Monk, engineering geologist, Tonkin + Taylor.
The team used data from 210 cone penetration tests (CPTs), 420 boreholes, 355 hand augers and 220 test pits to build the model. Detailed design started in October 2016 and is ongoing.
Using Leapfrog Works meant geological surfaces could be mapped by a geologist, rather than engaging a CAD technician to work alongside a geologist, resulting in a smoother workflow, and faster turn-around times.
As project engineers needed sections, they were able to go to a single point of contact to quickly create the desired section, saving time and need to re-produce work.
The model proved to be a good communication tool, doing away with the need for paper drawings.
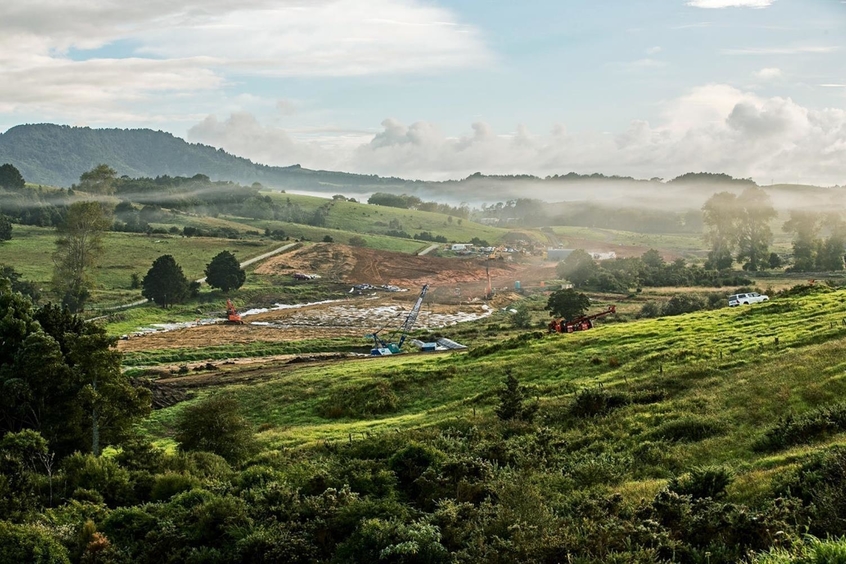
Ground improvements works (Courtesy of NX2 Group)
“By being able to show the model in 3D and cut sections at any desired location instantaneously enabled others to visually understand the geological conditions of the site with much better clarity,” said Stuart Cartwright, senior engineering geologist at Tonkin + Taylor.
“We collaborated much more as a whole project team as we were able to hold informal review sessions/workshops to show progress. In the past we would have gone with paper sections, but the 3D model outputs and graphical interface changed the way we communicated and collaborated,” Cartwright added.
He said the length of the proposed motorway and its alignment through such steep topography made the ground model development challenging.
The model was then imported into the Bentley OpenRoads civil design software, which allowed the slope profiles and cut and fill quantities for different alignments to be compared, to assess the most cost-effective alignment.
This helped reduce unnecessary cut and fill, while, reducing tree removals.
“Having a dynamic model that evolves as new data is provided has saved the team time from not having to recreate a new model every time, leaving us more time to focus on analysis,” said Chris Monk.
The motorway is expected to take five years to build and will be open to traffic in late 2021.
- Case study details supplied by Seequent.
Top image: The 3D subsurface model encompasses the full length of the 18.5km alignment (Seequent)