
Four recent graduates designed a living complex for the elderly built almost entirely of bamboo. They were supported by the Chartered Institute of Building’s Construction Innovation Scholarship, set up to promote quality of life through the built environment. It’s the first scholarship to be awarded in the programme. Tony Or is a candidate member of the CIOB.
Many countries in Asia and the Pacific region face an incoming “silver tide” in the form of an ageing population.
The Asian Development Bank predicts that the number of people over the age of 60 years in the region will triple between 2010 and 2050, reaching close to 1.3 billion people.
In Japan, it’s estimated that about a third of citizens will be elderly by 2035. In many cities, waiting lists for elderly public housing are growing.
We believe that a thoughtful approach should be taken to address the housing needs of these distinguished generations.
They deserve homes that are pleasant and accessible. Equally, the homes we build should be economical and climate-friendly. We owe it to all species and generations to avoid creating yet more carbon-spewing concrete forests.
For these reasons, we conceived and designed a three-storey apartment block made almost entirely of engineered bamboo. Our project was made possible by the Chartered Institute of Building (CIOB) through its Construction Innovation Scholarship, which sponsors research to improve quality of life.
We were supported by the Department of Architecture and Civil Engineering at City University of Hong Kong. The four of us are all recent graduates of the university, representing the disciplines of surveying, building services engineering, and structural engineering.
Why bamboo?
Bamboo is a promising, green structural substitute. Manufacturers can make elements including slabs, walls, beams, columns, and roofs through a process of sterilizing, steaming, compression and laminating. Engineered bamboo is composed of multiple layers of different thicknesses and grains to produce excellent strength and durability. It is highly versatile, lending itself to any number of shapes, sizes, and property configurations.
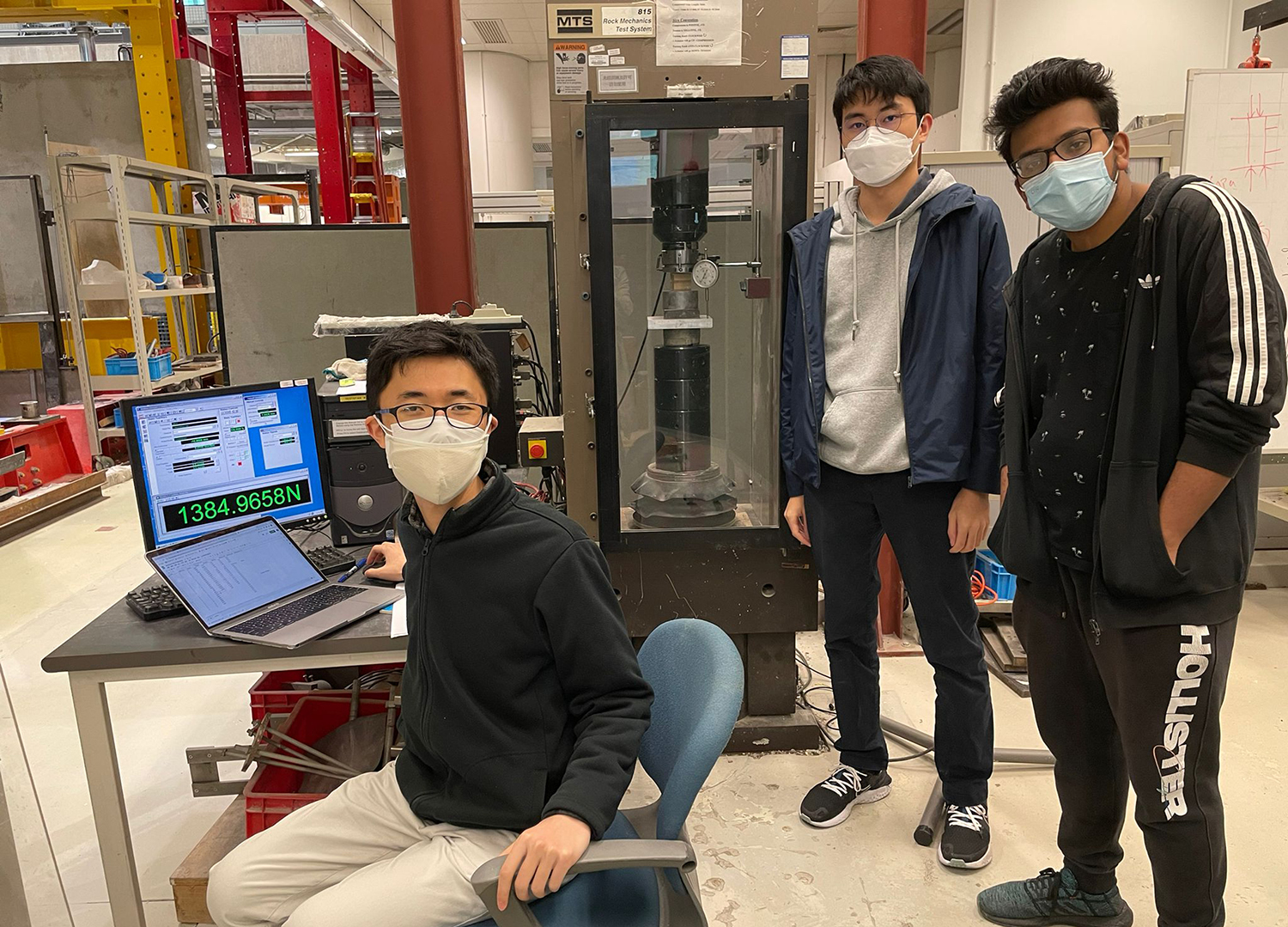
Its climate credentials are very good. This hardy, woody plant absorbs carbon dioxide all through its journey to maturity, and the energy needed to make engineered bamboo is far less than the energy needed to make concrete. Similarly, the emissions created by making it are small in comparison to concrete.
Unlike with concrete, bamboo requires no destructive mining for aggregate. Bamboo is widely available with many species common across Asia, Africa, Central and South America. It grows quickly and crop-yield is high compared to timber.
What we did
To create a realistic concept, we began with a literature review before moving on to design and calculation.
We created digital and physical models for the architecture and structure.
We tested the physical and mechanical properties of engineered bamboo elements to prove its suitability for residential structures.
Faster and cheaper
Our theoretical bamboo development was designed for a site in Yuen Long, New Territories, Hong Kong.
It consists of five, three-story apartment blocks, each 8,100 sq m in construction floor area and containing 44 one- and two-bedroom apartments on the first and second floors.
On the ground floors are social, dining, and reception areas. Roofs are used for building services and gardens.
Importantly, we designed the blocks to be built in a modular fashion, specifying prefabricated elements for faster construction.
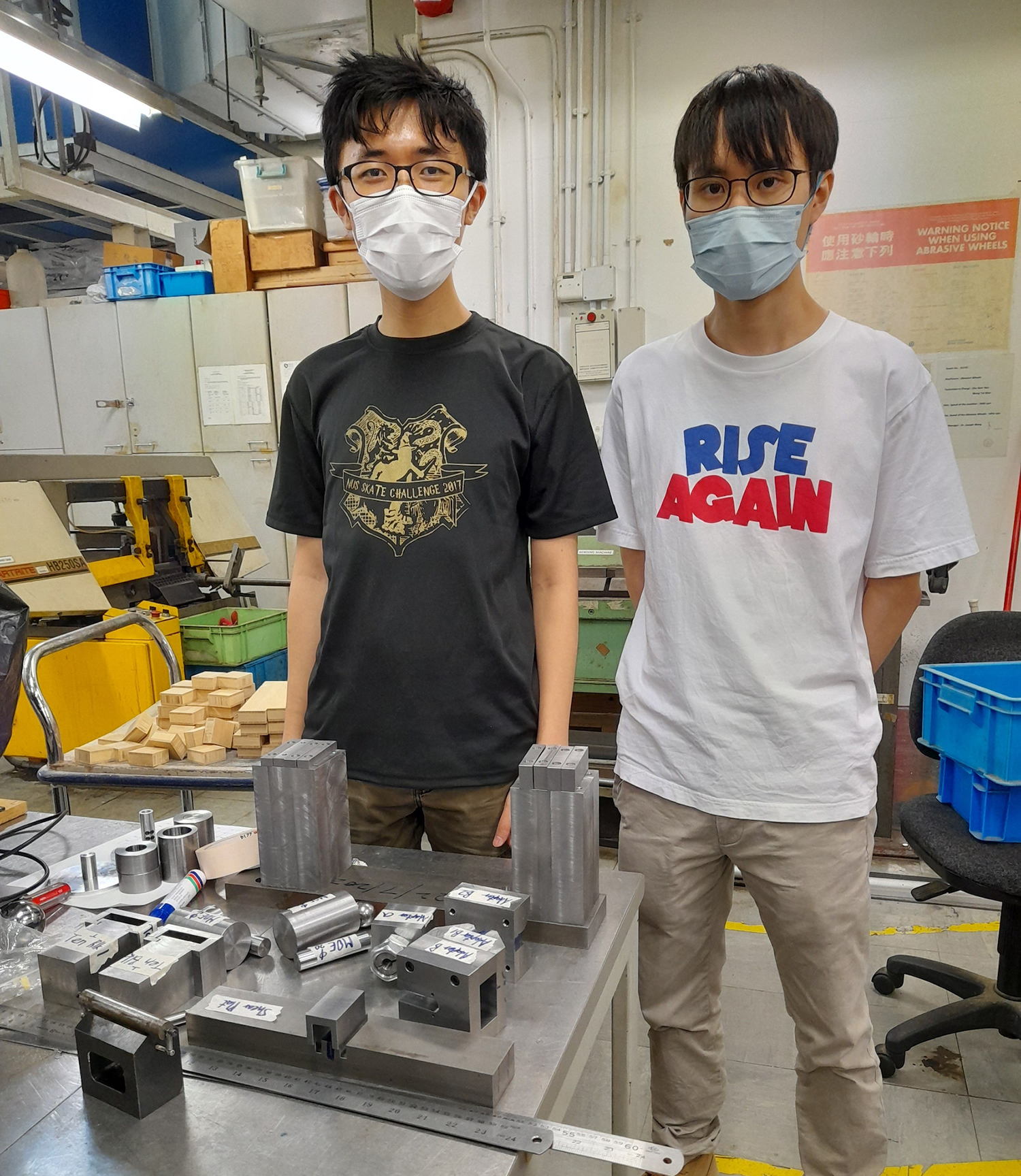
A number of bamboo suppliers currently provide engineered bamboo products. We used products from Bamboo International Limited for our physical models and for testing.
Compared to conventional concrete construction, we calculated that a non-modular bamboo building would take at least half the time to build and would save at least 30% of the construction cost. These savings are explained by avoiding concreting and formwork and the relative cheapness of bamboo.
If we use a modular approach with extensive prefabrication, the time and savings get even better: 30% less time compared to the non-modular bamboo scenario above and 10% less cost.
A more sustainable future
We believe at least one-sixth of older people in modern cities could be living in bamboo flats by the 2050s.
The challenge is to get government approval to build in this way. More research will help prove its suitableness, so local authorities could help by approving pilot projects.
With support from governments, developers will be more willing to adopt this sustainable building method and we could harness their commercial power and innovation.
It makes us glad to think our elders might enjoy tasteful, comfortable, and inexpensive homes designed especially for them instead of waiting precious years for costly and polluting concrete ones.
It was an honour for surveying-background alumni to receive this international scholarship for a large research project. We’re grateful to the Department of Architecture and Civil Engineering at City University of Hong Kong for supporting the modelling and testing.
• Our team was up-and-coming surveyor Tony Or, with Yik-ming Cheung (Ming), Crystal Zhao, and David Ng. We thank our supervisors, Prof C.W. Lim and Dr Ivan Fung, and our CIOB contract manager Ms Hassana Ahmed, Senior Qualifications Liaison Manager. Thanks also to Anderson Wai and Rishyanth Botcha for supporting the project’s delivery, measurement, and laboratory testing.