Building the Halley VI Antarctic research station in the planet’s most hostile environment took militarily precise planning, reveals the project manager.
Reminiscent of a giant robotic ant on skis, the structure is light, strong, compact, resists being buried by snow thanks to its aerodynamic shape, and it can be moved, essential since the ice it sits on is always shifting and could break away from the mainland.
But while much has been said about the innovative design, by Faber Maunsell and Hugh Broughton Architects, little has been said about how it was built – in the remotest and most hostile place on Earth.
Peter Willmott was there from the beginning.
Contracts manager at Galliford Try International, contracted to build Halley VI, he told GCR that because of the extreme conditions it was possible to work only during the short, summer season when temperatures creep up towards 0oC.
So Halley VI was built in just three 10-week seasons on site, spaced over four years.
Detailed programming
Materials and components from several countries were assembled in Cape Town and shipped to site in an ice-strengthened cargo vessel.
“In normal projects if you run short of something, you can have it delivered,” Willmott said. “Here every widget, every screw, had to be procured in advance. It came in two shipments, and that was it.”
Nor was it plain sailing once the ship pulled alongside the floating ice.
“We could load only six tonnes of materials at a time on the sledge,” added Willmott. “The total weight limit was nine tonnes, but the sledge weighed three. Over nine tonnes there was a risk of falling through the ice.
“The steel frames weighed nine tonnes, so we had to put temporary skis on the frames to move them.”
All the material was then sledged to the build site, 12km away. Each element had to be cased in a storm-proof box to keep out blowing snow and ice particles.
“We ended up with what we called our depot line, one line of materials sitting on the ice four kilometres long,” said Willmott. “We had a logistics manager who knew exactly where box number 12 was, for instance. And once you opened that box, you had to take the materials to the job site. You couldn’t leave it lying around because it would get buried in snow.”
Items in the depot line left over the winter were marked with GPS devices so they could be found and dug out of the snow each new build season.
“There was a great deal of effort in take-offs of materials and documenting them and scheduling for them to be installed,” Willmott said. “Very, very detailed programming.”
The team prefabricated as much as possible, including panels, bedroom pods and M&E cassettes.
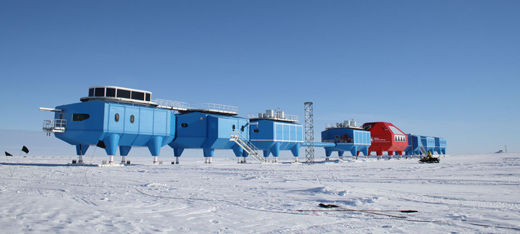
The crew rigged up a hand line so workers could find their way back to safety in a storm (Credit: British Antarctic Survey)
Extreme cold and wind
There were between 50 and 60 people on site during the build seasons, working a 12-hour day, six days a week.
Even though it was summer in the Antarctic, the cold and wind could be extreme and visibility very poor, so some days workers were confined to their accommodation.
“On one particular blow you couldn’t see more than half a metre in front of you,” said Willmott. “You can’t risk people working in that.
“The weather turns very quickly, so we had a hand line for people working on the modules so they could follow it back.”
After the second build season they had a weathertight envelope, with temporary heat, so work progressed faster.
Morale
Site accommodation was converted shipping containers, four people in each one, with two sets of bunks. “We lived and worked together 24 hours a day,” Willmott said. “Morale was important. Everybody was a long way from home. We were on tight schedules, and there was a lot of pressure.
“Everybody was very motivated but if people started getting disheartened it would spread like wildfire throughout the team,” he said.
Popping out to a restaurant was not an option, so good meals were crucial. The client, British Antarctic Survey, provided the hotel service and three chefs.
“There was very little in the way of fresh ingredients, everything was either frozen or dried,” explained Willmott. “But the chefs really tried and the meals were excellent.”
When the weather allowed a full week’s work they took Sundays off. On Saturday night the chefs would make something a bit special and the men would dress a little smarter. The normal limit of two drinks per evening was raised to four. Darts and snooker tournaments and penguin-watching trips also helped keep morale up.
Willmott said it would be great if all projects could be managed so thoroughly: “It’s a matter of persuading clients and persuading management that if you invest this money then you can have this kind of result. There’s no such thing as a free lunch.”