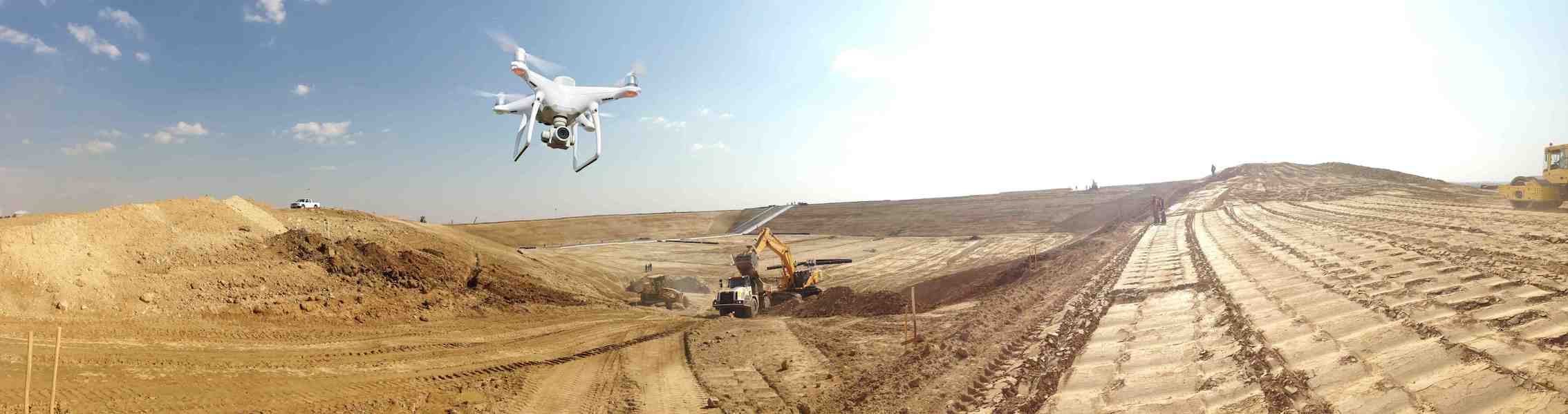
For most contractors, 2021 was about survival. A year initially expected to yield growth was hampered by labour shortages, supply chain rifts, and external project delays which kept non-residential growth weak for much of the year. In the US, across-the-board spending on construction this July was 11% down on pre-pandemic levels in February 2020, according to Deloitte.
However, the signing of the jumbo $1.2 trillion infrastructure bill has injected some much needed confidence in the year to come, with 91% of executives in construction and engineering characterising the outlook as positive, Deloitte said.
It’s great to see that emerging technology is baked into this unprecedented infrastructure push; the infrastructure bill contains $100m over five years to speed up the deployment of construction technology like digital twins.
Heading into what is expected to be a project-heavy few years, tech investment in construction is flourishing and data is at its core. Here’s what we can expect to see.
It’s no longer about more data, it’s about better data
Each time a new technology is added onsite, so too is a new layer of data. This data can be hugely helpful in uncovering new insights into improving efficiency and decreasing overruns, but add enough of it, and you end up with the opposite problem: too much data to wade through to find anything useful.
This is a point we’re quickly approaching. In just a few years contractors have gone from having very little data to nearly drowning in it. Technology products should lead people to answers, rather than just leaving them to extract insights on their own.
Surveyors are becoming the designated data analyst on the job site, expected to manage data from various measurement technologies. If the construction tech industry’s approach to data doesn’t become more curated and unified, surveyors could go from being stuck in the field all day measuring, to being stuck behind a desk all day managing a litany of different softwares.
New measurements mean new benchmarks
The influx of digital technologies is giving contractors data on things they’ve never even measured before, allowing them to draw new correlations. A half-centimeter discrepancy in ground level from one week to the next, or a specific run pattern for equipment, may lead to a project-delaying consequence in 90% of cases for a given contractor.
What gets measured gets managed. The availability of a mass of new jobsite data will lead contractors to develop new benchmarks and thresholds to meet on all elements of the site from initial earth-moving to building. These benchmarks will be set over time, as project-to-project data begins to be analysed for patterns of efficiency as well as data indicators of a forthcoming error. It’s likely that the largest contractors globally will be the ones leveraging this kind of metadata in the near term, but it will prove a powerful differentiator.
Data will unify teams from project start to finish
Just a few years ago, it was industry standard to have a project head go out and walk the site to kick off a job. They would then meet with different teams to give them the lowdown on the space and potential challenges they could face.
Every team has their own unique concerns and, in many ways, speaks their own language, making it necessary to have many individual conversations. Unfortunately, this method is also inefficient.
The next year will be a testing ground for a new communication model on site — one driven not by words but by data models acting as a single source of truth that every team can inherently understand.
Drones and similar measurement technologies have the capability of producing 2D and 3D maps of the worksite, which every team can access remotely and interact with to aid decision-making. Not only do these single sources of truth save time in communication, but they also share more information than trying to verbally explain a jobsite ever could.
Put simply, data is the currency nearly every industry is operating on as we look to the future. Contractors will benefit from this influx of information as soon as they’re ready to put it to use, and those who do, will have a leg up on the year, and many projects to come.
- Mike Scott is regional manager at Propeller Aero, a construction drone analytics firm