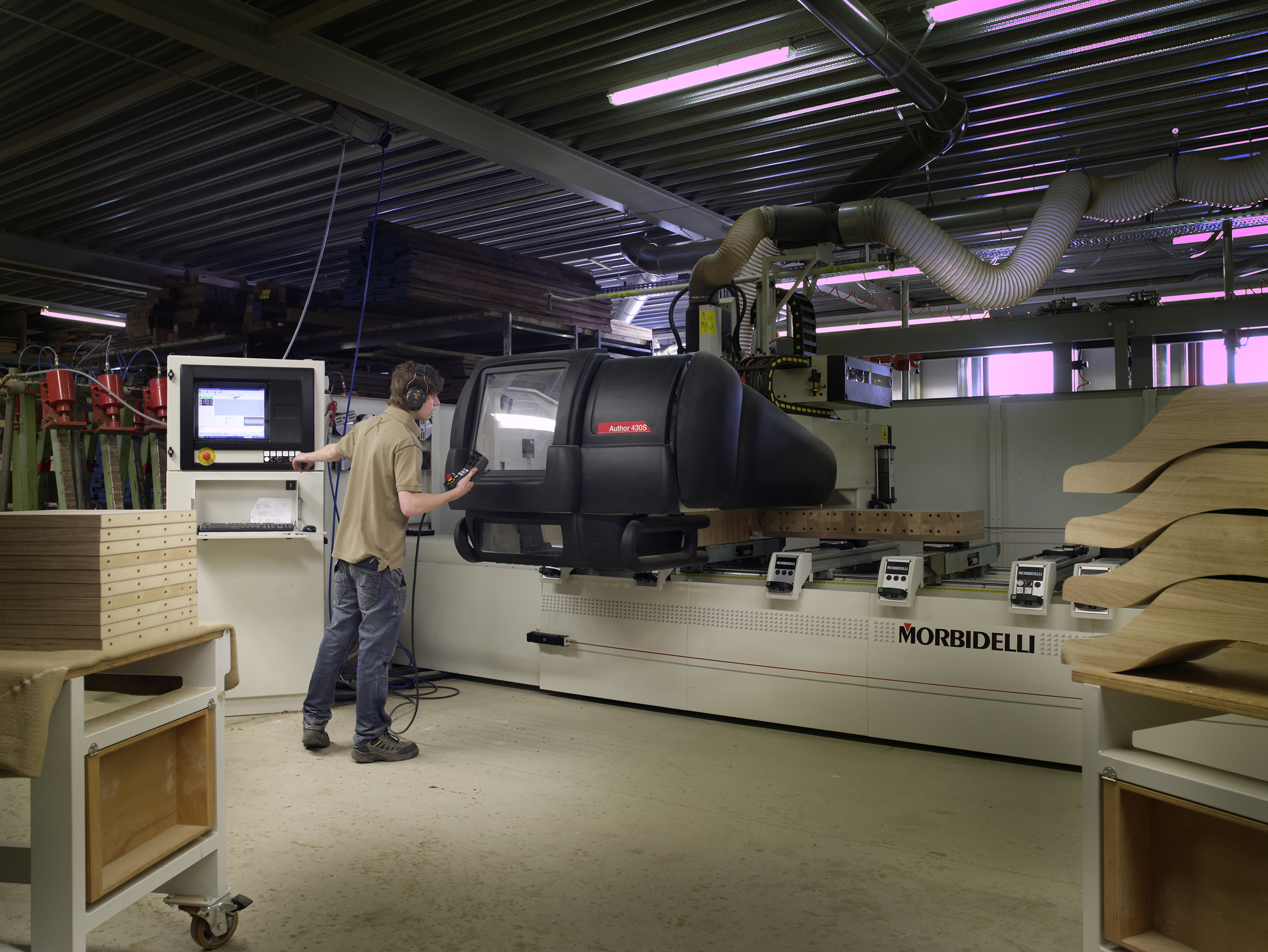
The brief, dazzling life of Katerra – the American start-up that claimed to have revolutionised construction with its tech-driven approach to mass prefabrication, only to collapse completely in June last year – will have confirmed for many the suspicion that construction can never properly industrialise.
But the dream is far from dead, and investment still pours into construction technology start-ups.
One of these is Slate Technologies, founded in the same year as Katerra’s demise to give general contractors an AI-enhanced software platform to help with scheduling and decision-making.
Its rise so far has been impressive: it has completed all the funding rounds it needs and claims to be working on many projects from healthcare to residential. It has around 50 employees and Californian offices in Pleasanton and San Francisco; others are in Bangalore, Guadalajara and Toronto.
Last month, Slate took over digital designer, Splash Modular, which has spent the past three years developing a digital design and fabrication process for customised bathroom pods.
As part of the deal, Splash chief executive Joel Hutchines moved from North Carolina to California to become Slate’s head of industrial construction (IC). GCR talked to him to find out what direction America’s lively digital construction industry is taking post-Katerra.
Splash’s big idea
Hutchines describes his former company’s concept as a kit of parts, each of which can be made using digital fabrication. “We scripted that bathroom pod and what we could then do was send a file to manufacturers,” he says. “That became the way for us to productise our process and licence the assembly to somebody else.”
That meant the initial design was geared to automated digital fabrication, which in theory optimised the entire design, fabrication and assembly process.
Joel says: “There’s a big efficiency gain for suppliers in IC. Contractors usually receive design intent from the architect and redesign it to make it work. Scripting allows us to avoid that. We get the data in the hands of a designer early so they can work within the realm of what’s achievable, then from a supply perspective they can automate the entire process.”
This means that, rather than having a library of one-off designs, there is one script that is essentially all the designs in one. Joel says this offers “huge economies of scale, even with mass customisation” since it doesn’t matter whether the machine is cutting a circle, square or triangle.
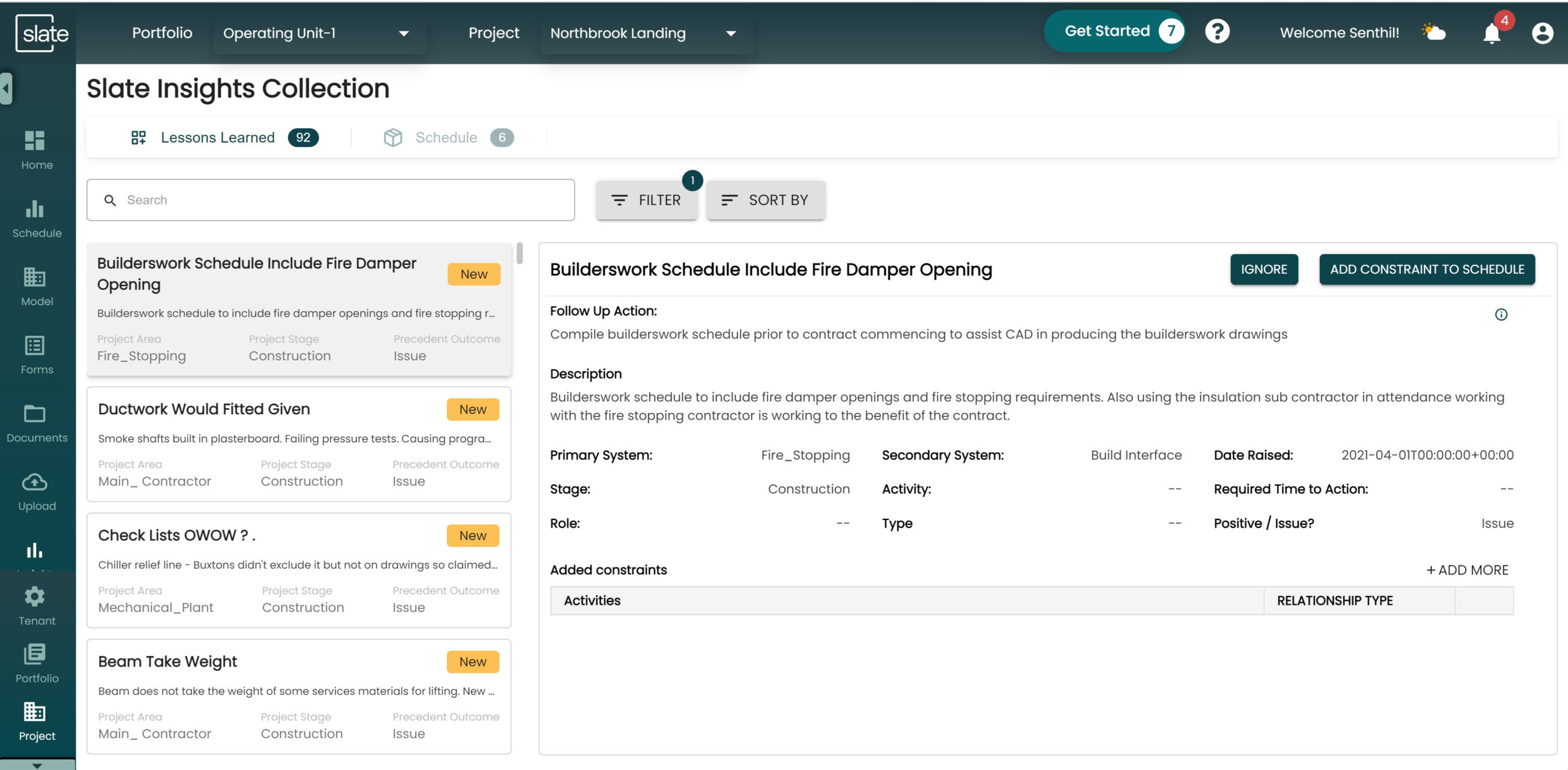
The ability to customise production means that instead of investing in a production line to make bathroom pods and hoping for enough orders to recoup the investment, the supply chain can use the agility afforded by digital fabrication to adapt itself to whatever design is required – within certain parameters, of course.
Another advantage is that the system can be integrated into the building information model (BIM). Splash launched its original marketplace of components within the BIM, allowing an architect working on a 3D design to access data for project delivery and the availability of suppliers.
“We launched our configurators within BIM so we could guide architects,” Hutchines says. “BIM has been slow to be adopted and it never really saved the industry like it was meant to but I think it all comes down to data, and that’s something that Slate can really help with. We can share data within Slate already and we have the ability to take in BIMs and apply attributes to them, so you can interact with BIMs within Slate.”
The fate of Katerra
But does a sufficiently large digital manufacturing base presently exist to meet the demand from digital designers?
“Traditionally, no it doesn’t,” he says. “But we’re seeing more and more sophistication in and around these suppliers. I saw this at a recent advanced prefabrication conference, even on the mechanical, electrical and plumbing side. We’re starting to see far more industrialisation so there’s the option of automation on that side, but also a lot more digitisation and scripting as a service. We’re presently working with US suppliers and also contractors in the UK and suppliers in Australia.”
This reliance on an evolving IC ecosystem was something that Katerra decided to avoid. As with Splash, it was based on the idea of using a digital platform to integrate design, manufacture and assembly. When it formed in 2015, its founders preferred a vertically integrated business model in which it employed architects, contractors and eventually operated three factories. For a while, it seemed to work: by 2019, it was valued at $4bn. However, two years later it filed for bankruptcy protection and sold its factories – one of which, in Spokane, Washington State, contained one of the largest cross-laminated timber presses in the world.
To some extent the collapse was caused by bad luck: a combination of the Covid-19 pandemic and the collapse of Greensill Capital finance company wrecked the company’s balance sheet. And to some extent it was due to a failure to turn theory into practice: digitisation did not slay the construction dragons of delays and cost overruns.
But Hutchines thinks Katerra can be counted a success in some respects. “They paved the way for IC and they drove a lot of investment into the sector,” he says. “They started to bring to light how much benefit there could be. I’m full of praise for Katerra and the people who were involved. When I started Splash Modular it definitely helped people to listen to what we were saying. It was a shame what happened, but it helped the sector in the US to evolve.”
He wonders, too, whether Katerra was right to go for vertical integration. “I’ve preached the advantages of a decentralised supply chain and localised assembly. But there is merit to vertically integrated models. Maybe if they should have been more vertically integrated – taken on developers as well? From my perspective, if you leverage computational design and digital fabrications you can start to have a structure like the automotive industry, based on a network of suppliers.”
Next steps
It may have been that Katerra was just born too soon – before the manufacturing, construction and tech industries were ready to play their role in the system. So, what developments can we expect in the future?
To answer this question, Joel refers to his new role with Slate Technologies, and its development of an AI assistant to help project and construction managers make better operational decisions.
He says AI should process large amounts of complex data from multiple sources to offer “multi-criteria decision assistance”.
In that vein, Australian company Archistar has software that can look at town planning and site constraints and present options. Slate’s product could, for example, help a project manager decide when to carry out a concrete pour. Factors in that decision could include weather, traffic, lessons learned from similar pours, whether the Miami Dolphins are playing a game, and more. Then there is “dark data” – data collected by an organisation but never analysed and processed into useful information.
“We can really quantify what all those factors mean before, during and after the decision,” says Hutchines.
As we know, where there is AI there is also ML – machine learning. However, it’s often noted that where there is ML there is also BD – big data. At present, it’s doubtful whether the construction industry has gathered enough multi-criteria situations to really train its AI, but this can only improve over time.
Further reading:
- Four senior Katerra women lead US expansion of modular builder, Modulous
- Intelligent City opens first robotic urban housing factory in Vancouver
- Bankrupt modular builder Katerra sells factories to rivals
- Why Katerra’s demise shouldn’t deter construction’s innovators
- Latest offsite construction “disruptor” takes on heavyweight tech staff