Architects hoping to play with large, free-form concrete structures often get sent back, literally, to the drawing board because the complex timber formwork required is so expensive. But now a new, “inflatable concrete” system developed in Austria could restore some of that freedom by removing the need for formwork altogether.
Researchers at the Vienna University of Technology (VUT) this month announced the successful demonstration of a system that uses air cushions to push and bend newly-poured concrete slabs up into predetermined shapes.
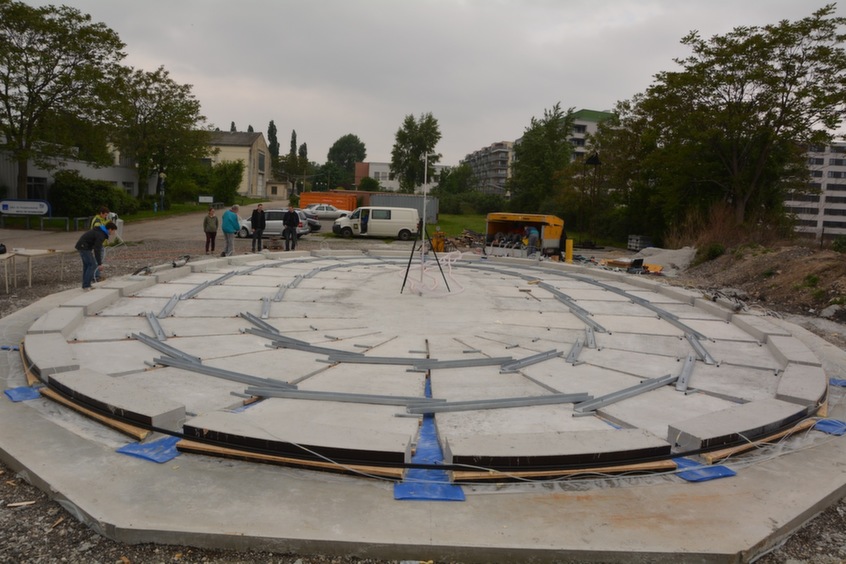
The plane concrete plate is produced (VUT)
Called the “pneumatic wedge method”, the technique is fast and relatively cheap because it requires no formwork. An experimental structure has now been built using it.
First a flat slab consisting of several segments is poured with standard concrete. Spaces are left between these segments so they fit together when the structure is bent. 
It is crucial to get the geometric shape exactly right.Â
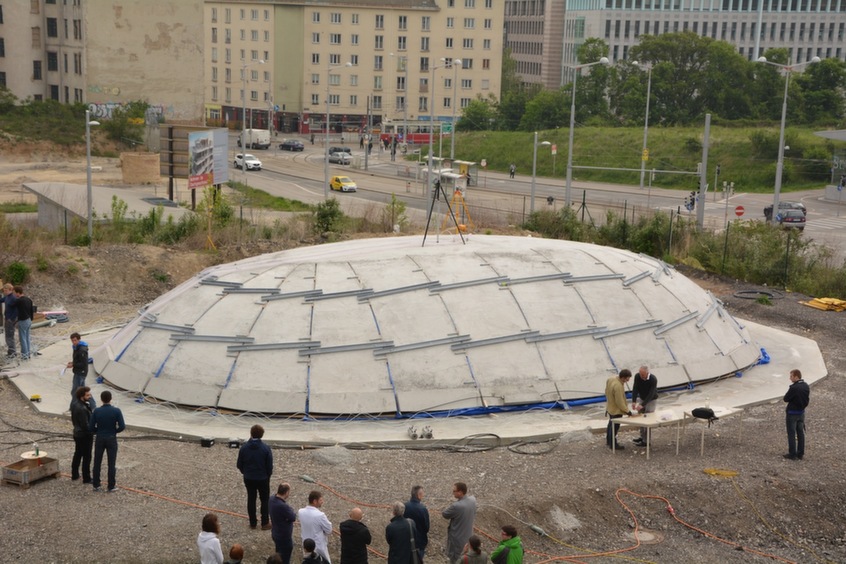
The airbags are inflated (VUT)
Once the slab is hardened, an air cushion underneath is inflated. At the same time, a steel cable is tightened around the concrete segments, so that the concrete is lifted up in the middle and pushed together at the edges.Â
The concrete segments are connected with metal beams so that they move together as required. In the experiment, it took approximately two hours to “inflate” a 2.9m-high concrete shell.
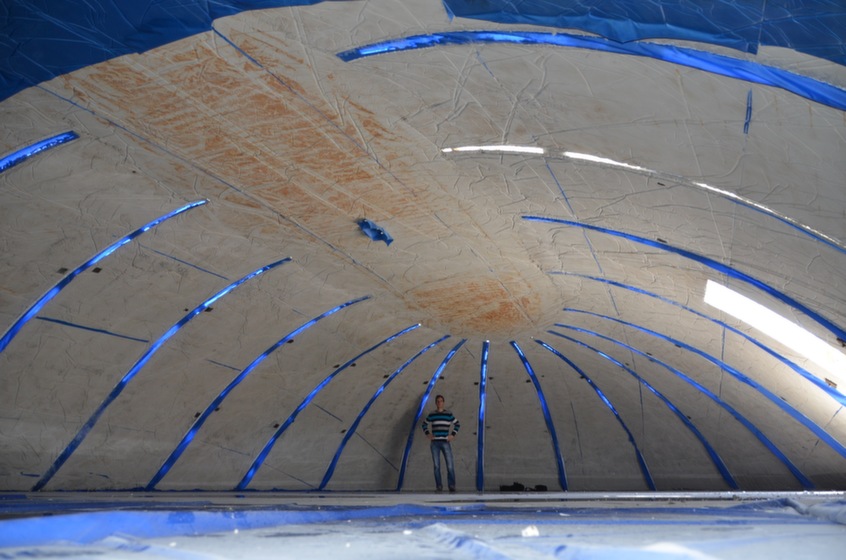
The completed dome inside with a room height of 2.9m (VUT)
The researchers say that when the concrete is bent many tiny cracks appear, but that this poses no problem for the stability of the shell. “We can see that in old stone arches”, said Johann Kollegger, professor at VUT’s Institute of Structural Engineering. “If the shape is right, each stone holds the others in place and the construction is stable.” When the structure is rendered it has the same properties and stability as a concrete shell built with expensive formwork, he added.
The pilot building is an elongated sort of dome to show that more complex shapes can be made. “Building shells with a diameter of 50 meters is no problem with this technique,” Kollegger said.Â
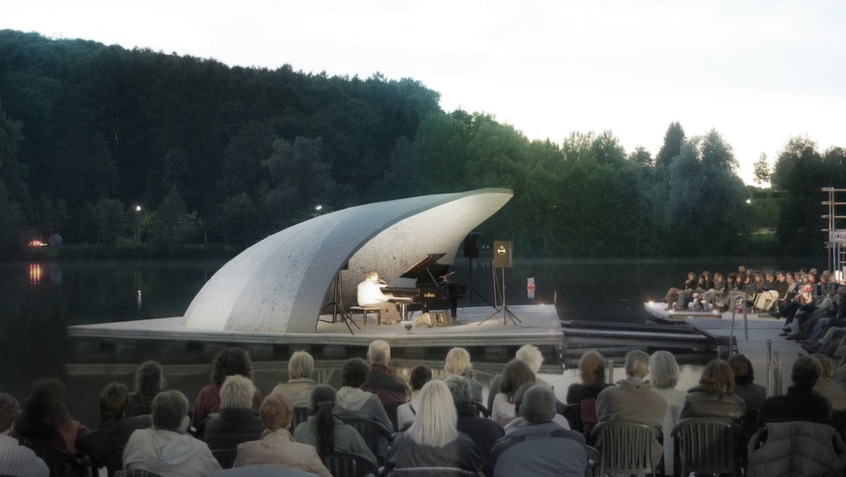
A possible application make a concert shell (VUT)
His colleague, Benjamin Kromoser, estimated that doing away with the formwork cuts out around half of the construction cost, and the savings would be even greater for bigger structures.
The team hopes that the new construction method, which has already been patented, will be taken up by the market.
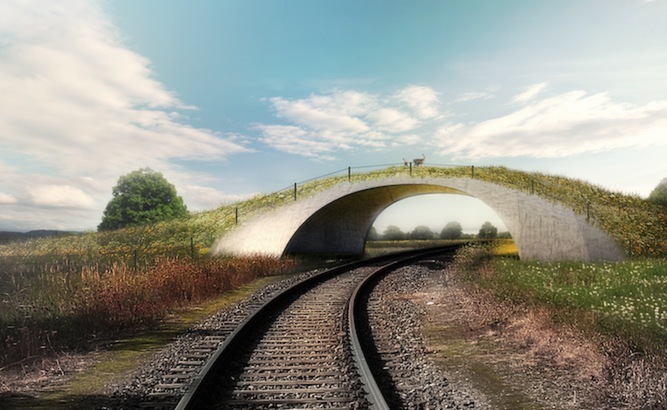
Rail overpasses may be another application (VUT)
Meanwhile Austria’s federal rail body, OEBB-Infrastruktur AG, has commissioned a design based on the new method for a deer pass over two high speed rail tracks in Carinthia.
The technology was developed in a research project managed by the Austrian Society for Construction Technology and financed by the Austrian Research Promotion Agency. Industrial partners included Strabag, Bilfinger Berger, Sika Österreich, and others.
Comments
Comments are closed.
Comment
I would suggest the rail overpass bridge in photo above will require quite a lot more inflation before a train can pass under!
This idea is not new (but may be an adaptation on the previous). I understand there were six domes built in this country using the inflation technique, some used as salt stores at the side of motorways, but both Cheltenham Girls College and Mildenhall Technical School used them as Sports Domes. Unfortunately the dome is an echo chamber and any noise created inside (as in pupils playing sport) reverberates endlessly.
I am excited to think about the possibilities rather than leave a negative comment – let’s start celebrating our ideas as an industry and comment with collaborative suggestions and shared experiences.
fantastic – i would reckon however, a natural and simplified progression of this concept could be fully inflated (to the permanent shape) form work with layers of flexible mesh reinforcement applied and then concrete sprayed on to the structure?